Disrupt.Design Lab develops the WoodenWood Stool: Utilising a digitally fabricated woven surface derived from sawdust.
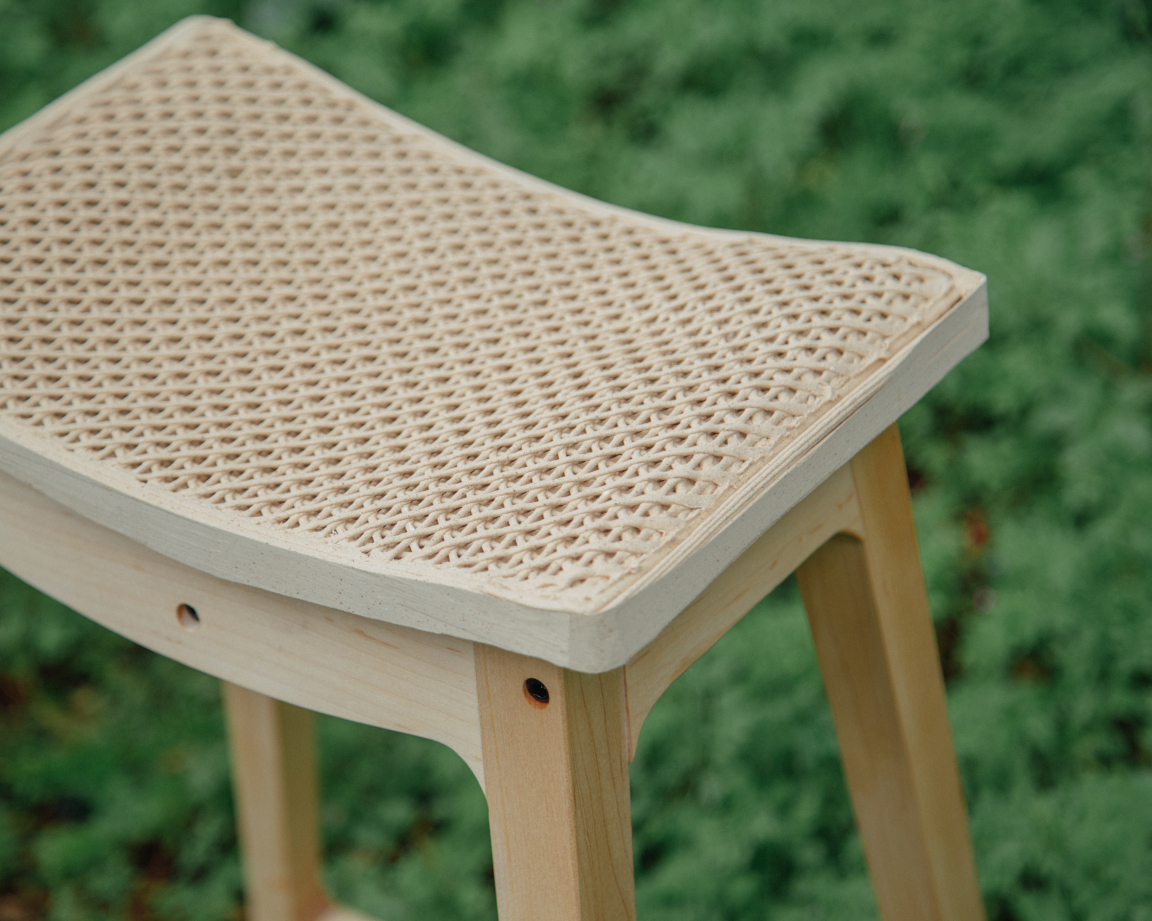
Photo credit: Disrupt.Design Lab
How can we combat the waste of the wood industry? According to Disrupt.Design Lab, by 3D printing with sawdust.
Closing the loop in this industry is the WoodenWood project, which through applying a blend of both traditional and digital fabrication with circular design theory has developed a closed loop, zero waste stool.
Wood is one of the most prevalent building and industrial materials, yet despite being a natural material with potential for reuse, renewal, and biodegradability, the lifecycle of wood today is far from circular, with the industry generating millions of tonnes of wood waste annually. Tackling these tonnes of unused 'waste' is Disrupt.Design Lab, with its 3D printable ‘wood paste’.
Disrupt.Design Lab is a platform for design-led technological research for enhancing the sustainability of the built environment. Founded by the Faculty of Architecture and Town Planning at the Technion - Israel Institute of Technology and led by architect and professor, Shany Barath, the lab brings together a dedicated and diverse group of researchers that observe global environmental challenges and exchange ideas on formulating circular material directions for the built environment sector.
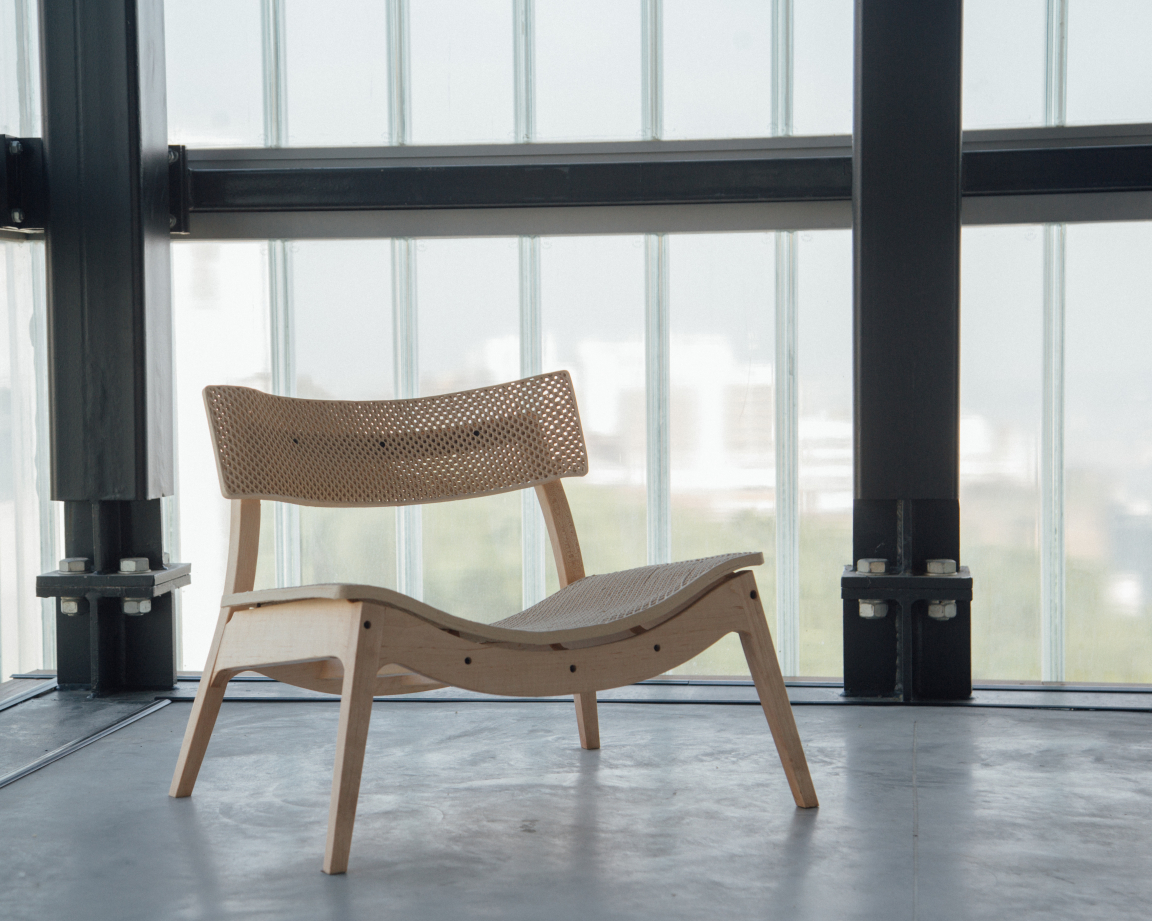
Photo credit: Disrupt.Design Lab
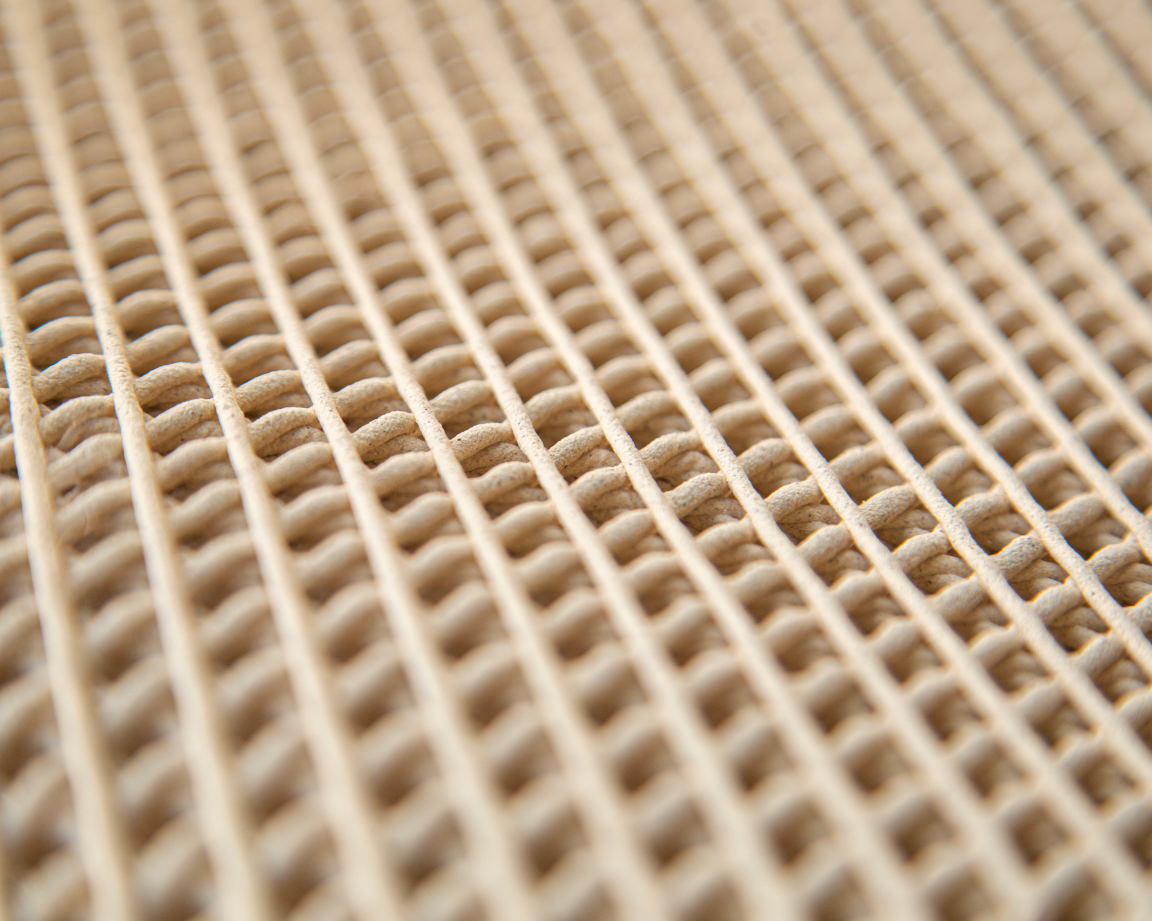
Photo credit: Disrupt.Design Lab
Serving as a launchpad of knowledge between academia and industry, Disrupt.Design Lab’s most recent material exploration, the WoodenWood project, employs circular design solutions for wood products and processes.
By integrating both traditional modular woodworking and digital robotic 3D printing of a natural wood paste, the lab has achieved successful prototyping of circular wooden seating.
The printing tool path creates a new ‘wood-textile’ - simulating a rattan textile - while using an often overlooked material, sawdust. The raw wood structure serves as the mould for the printing process, avoiding additional waste through by-products.
The wood paste prepared for printing is derived from ‘Daika’, sawdust with cellulose-based natural binders to enable 100% biodegradability. A parametric model and manufacturing workflow have been developed by the team to to correlate between the chair geometry, robotic toolpath, and material properties.
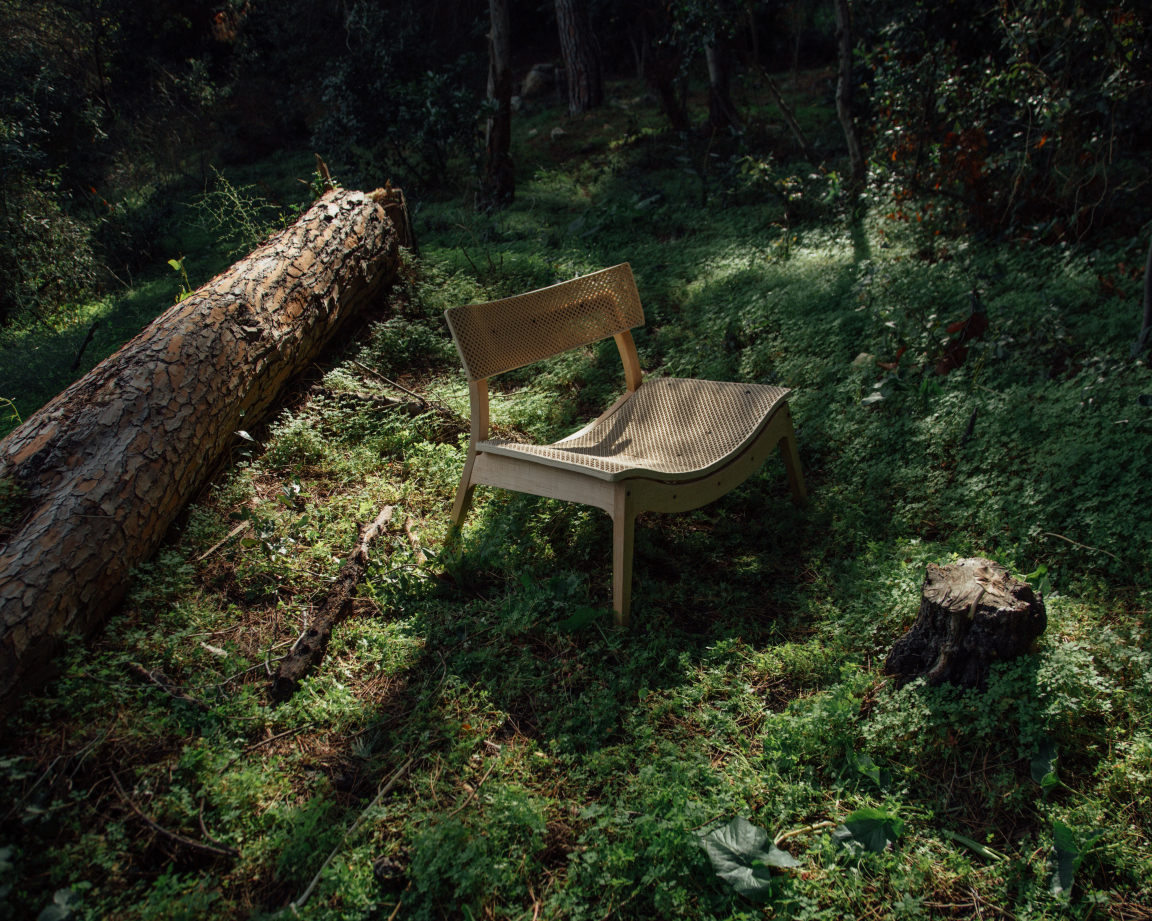
Photo credit: Disrupt.Design Lab
The results are examined for strength, elongation, visual expression, and geometrical compatibility in order to customise for human comfort. Through this process, a multitude of possible designs can be explored to create a ‘one of a kind’ chair within a mass production workflow.
While the solid, traditionally crafted structure supports the 3D printed seat of the chair, the printed sawdust completes the weaved back and seat. Combining two lifecycles of raw wood and sawdust through the fabrication of the WoodenWood chair, the product demonstrates a circular design expression of wood towards zero waste.
The efforts of Disrupt.Design Lab were recognised at Milan Design Week 2023, earning a mention as one of 12 projects in the sustainability category by Fuorisalone. Furthermore, the Design Educates Awards 2023 jury selected the project for a gold prize in universal design, and the team as the emerging designers of the competition.
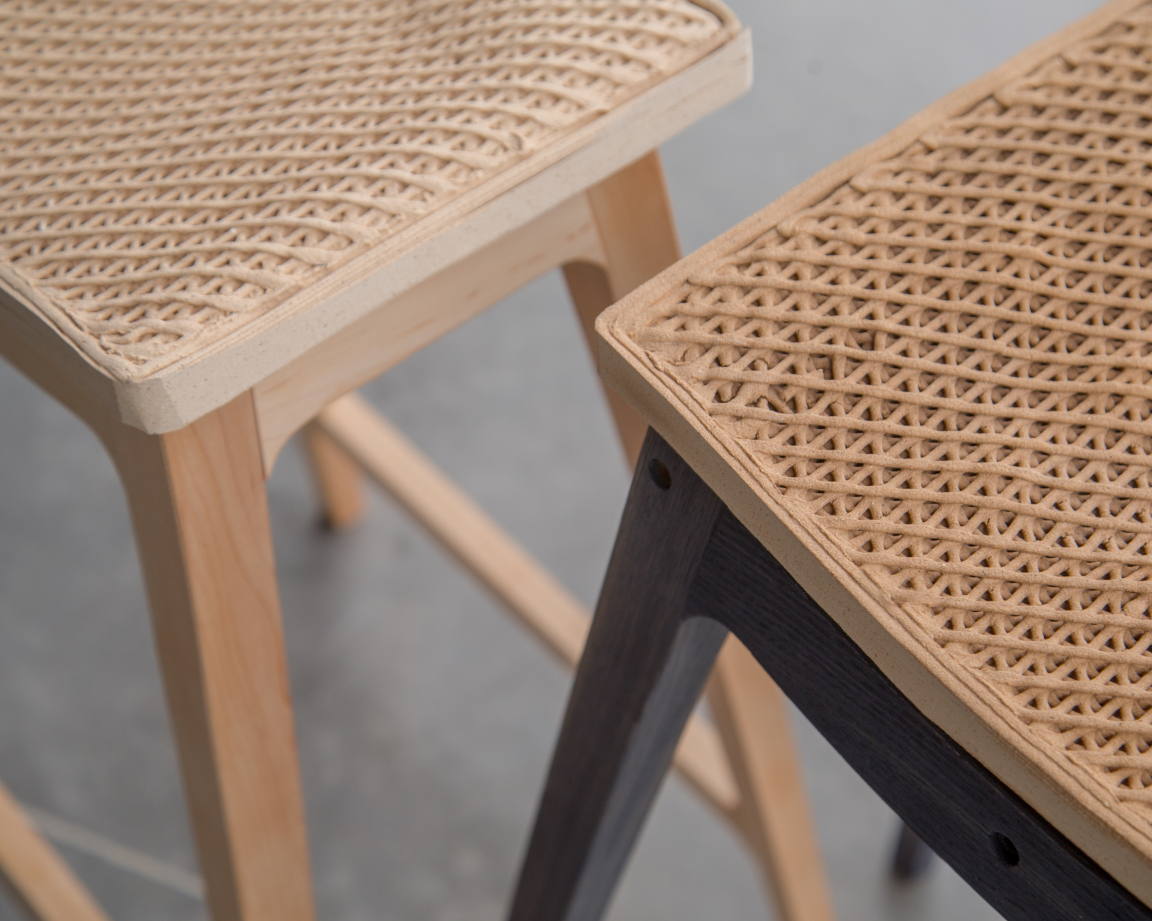
Photo credit: Disrupt.Design Lab