Lucy Black, head of business development, K-BRIQ on the closed-loop, un-fired, ultra low embodied carbon brick - a circular solution for the built environment.
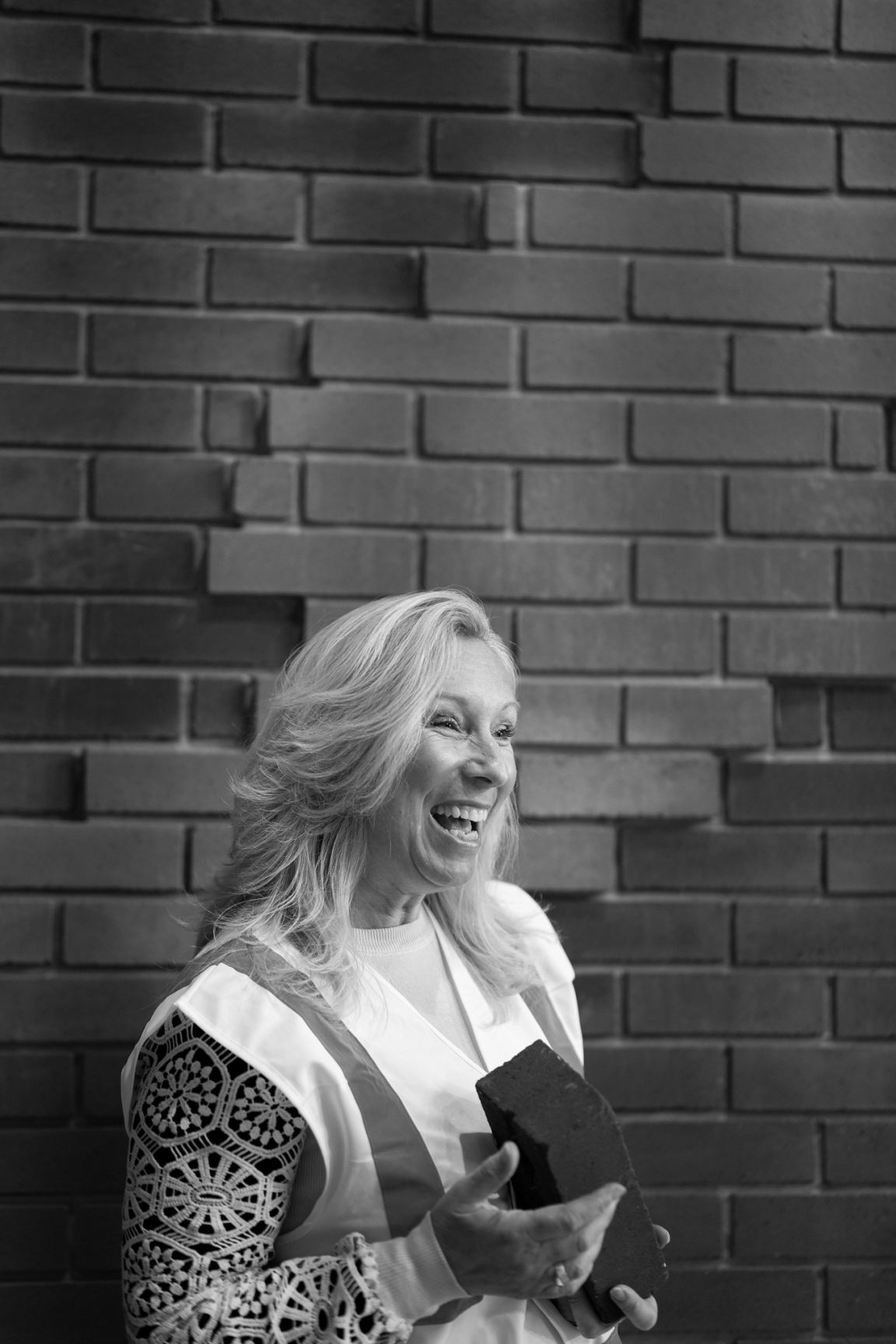
At present, the built environment is one of the most linear of industries; responsible for mass consumption of natural resources, generation of waste and a mass emitter of carbon emissions on a global scale. But, solutions are on their way. And fast - according to head of business development at Kenoteq, Lucy Black.
Kenoteq is harnessing these key environmental challenges as opportunities. First breaking ground in Edinburgh, the K-BRIQ holds itself a high competitor to the traditional clay and concrete masonry bricks - boasting a 95% lower carbon footprint, and near 100% re-directed demolition waste content.
As we race towards achieving Net Zero, Kenoteq is tackling the critical challenge of legislation-based carbon targets through its speciality facing brick. Available in a variety of thirteen different stock colours - all made from recycled pigments - the team also offers specialist colour mixing and a matching service to ensure flexibility and a sense of individuality for designers.
Here, Lucy shares with us the research and development that has gone into un-fired, circular economy brick, the projects and new products currently in the pipeline - spanning slips, flooring and paving options - and Kenoteq’s mission to build a closed-loop, locally supplied circular economy model for the built environment.
Firstly, could you please introduce us to Kenoteq and explain how it came to be?
“Kenoteq was established in 2019 as a spin-out from Heriot Watt University in Edinburgh on the back of nearly a decade of research and development into the circular, closed loop, ultra low carbon K-BRIQ.
“The K-BRIQ is science-based, grounded in research from Heriot Watt University. The final product being a collaboration between Heriot Watt University and one of Scotland’s leading construction waste management companies, Hamilton Waste & Recycling - who provide our recycled gypsum.”

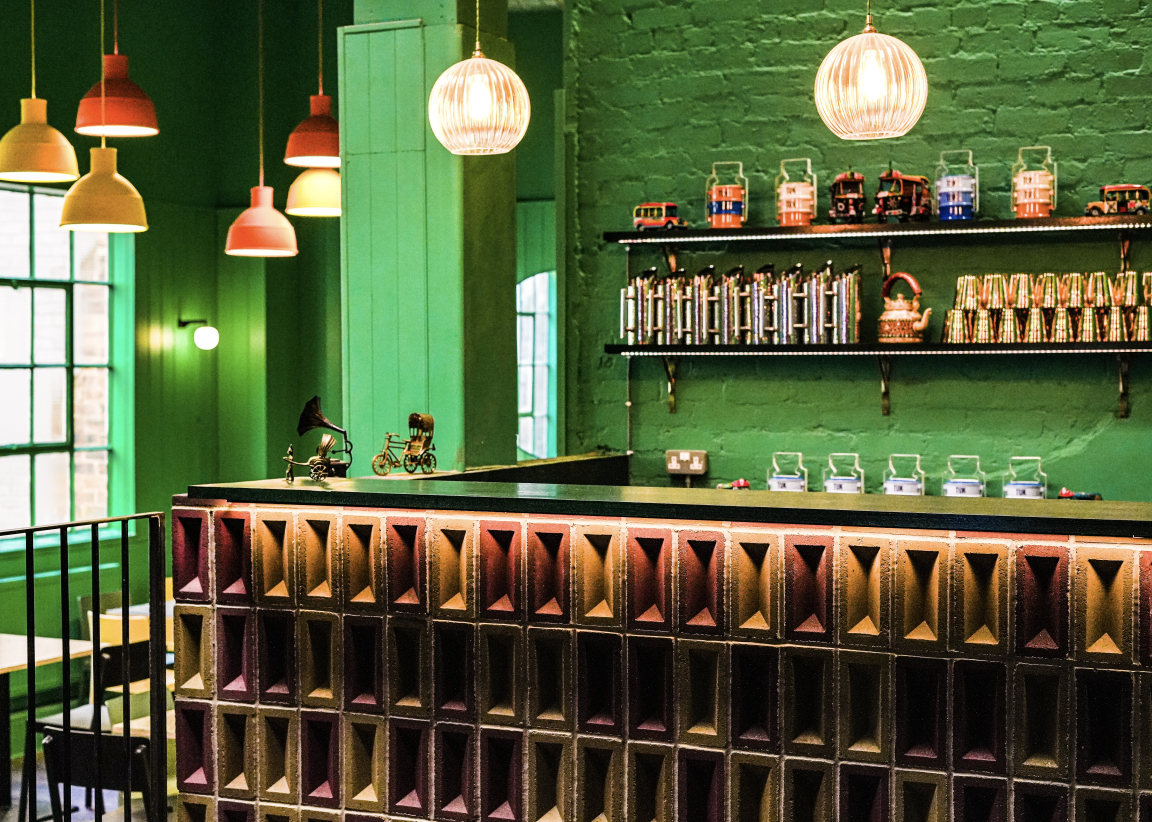
Tuk Tuk Restaurant, Edinburgh
Now, let’s hear about one of the most innovative construction bricks to enter the market, the K-BRIQ. What was the motivation behind its development?
“The construction sector and built environment boast three unfavourable issues that need to be challenged; (1) The construction sector is the largest consumer of natural resources through the energy-intensive extraction of sands, clay, stones and gypsum, (2) the sector is the highest producer of waste in the UK, and (3) the built environment is the greatest emitter of carbon emissions globally, contributing nearly 40% of all global carbon emissions. We set out to provide sustainable building materials that provide a solution to these key societal challenges.”
What is the K-BRIQ manufactured from? And what's the process?
“The K-BRIQ is made from near 100% recycled waste. The majority of the waste is from certified inert recycled aggregates - such as rubble from old brick, old stone, and old mortars - together with recycled gypsum from waste plasterboard. We also add recycled pigments to colour the product and a dash of our proprietary binder - our “secret sauce!” - to help bind the product.
“We work with two local waste management partners who collect, sort and process construction and demolition waste to strict protocols. They provide it to us as certified inert processed waste streams to manufacture into the K-BRIQ and K-SLIPs at our clean-tech factory outside Edinburgh.
"Our patented low energy production process uses hydraulic compression and is efficient, creates no waste and uses only 10% of the energy of traditional brick production. Our whole production process takes only 24 hours, significantly quicker than traditional brick production.
“Importantly, we do not fire the products - which gives us an enormous energy saving and reduction in carbon emissions. In fact, the final embodied carbon (the carbon footprint) of the K-BRIQ is under 20g CO2e per unit, which is 95% less than a traditional clay brick. In comparison, a traditional brick has 455g CO2e per unit (sourced from the Brick Development Association EPD 2019-2024).
“Going forward, Kenoteq’s expansion model is to set up production regionally across the UK, and eventually internationally. Our process will provide a local solution to the construction waste issue, reduce the need for long carbon-intensive journeys transporting waste and heavy materials both to and from sites, create local jobs and support local supply chains. Most importantly, it will reduce carbon emissions locally for a cleaner environment in which to work, rest and play.”
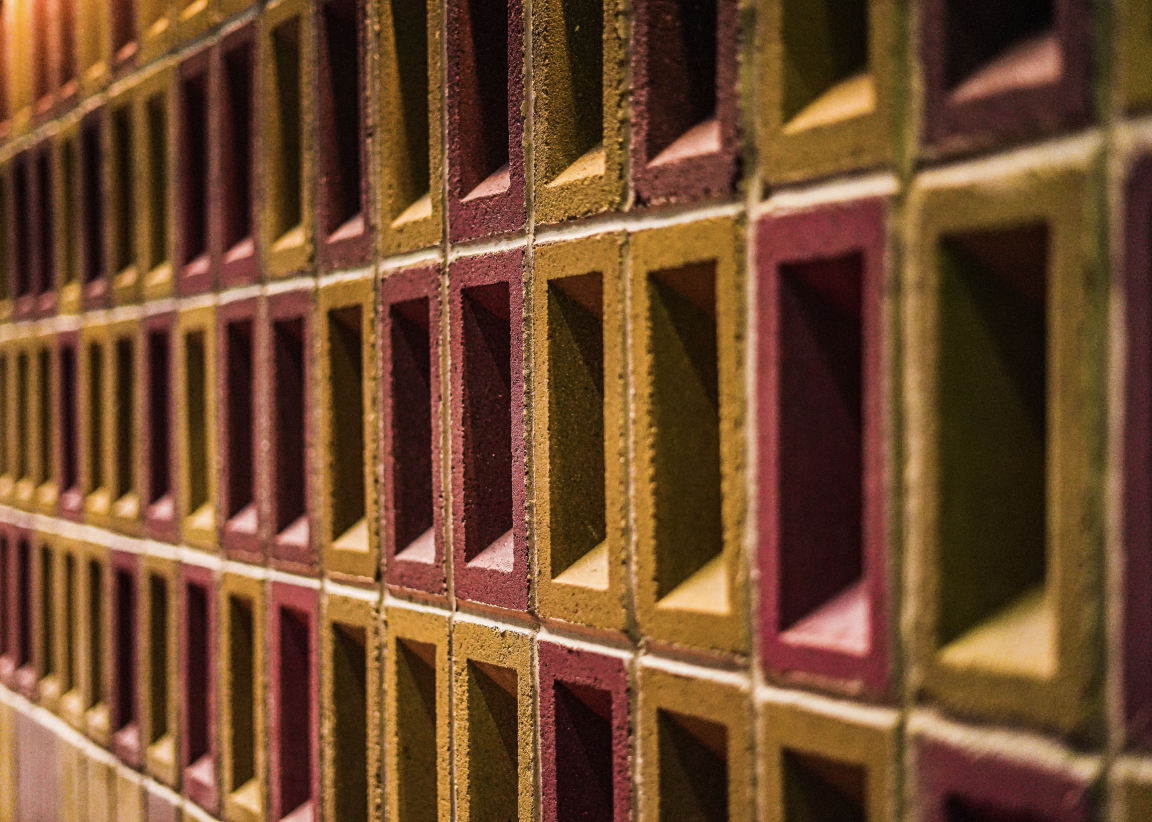
Tuk Tuk Restaurant, Edinburgh
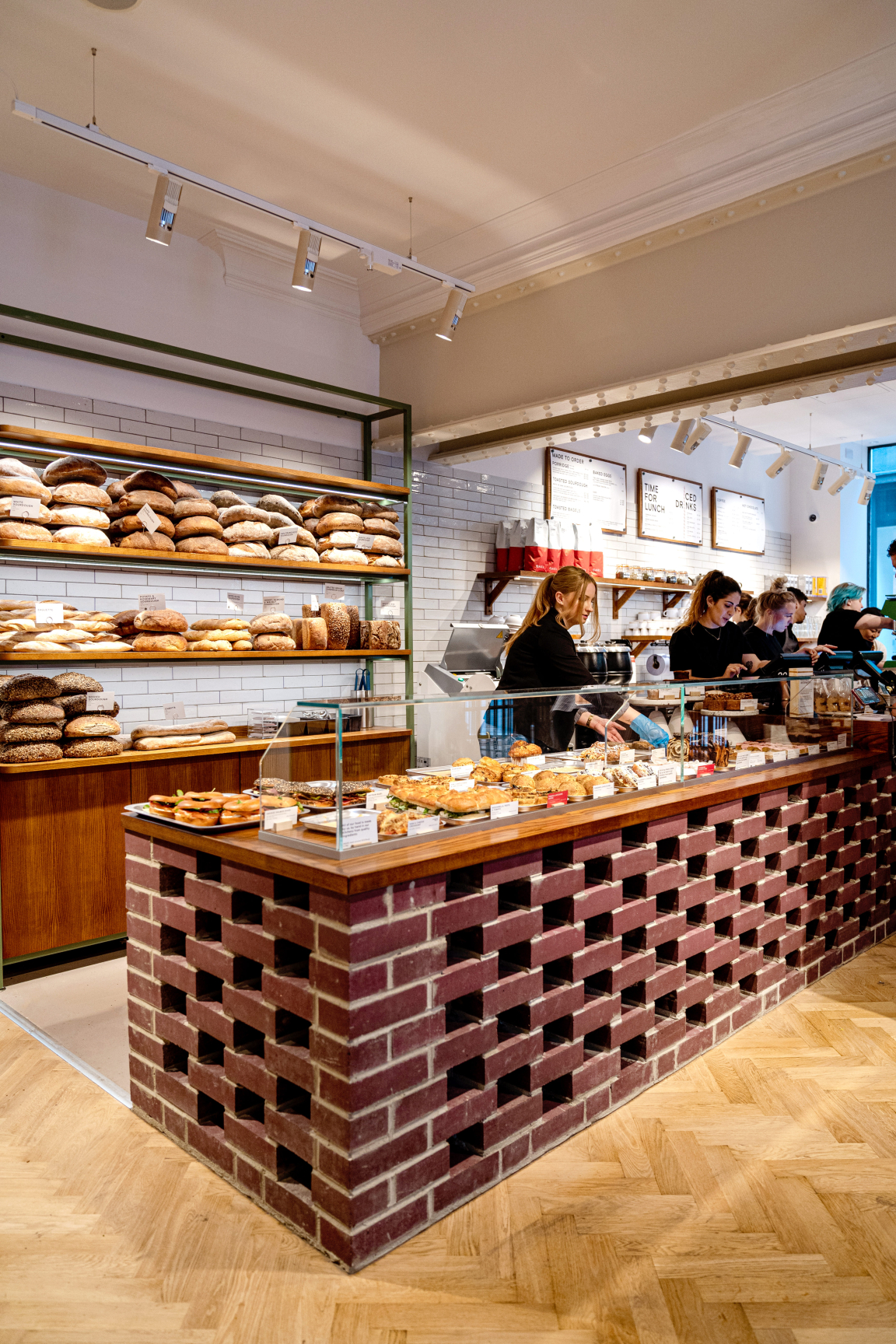
Gails Bakery, Manchester
Could you share with us some case studies where the KBRIQ has been utilised?
“As the K-BRIQ awaits certification, projects have been limited to demonstrators, exhibits and interior features. There is a well documented demonstration wall built in our magenta K-BRIQs for COP26 in the Innovation Factory at Built Environment Smarter Transformation (BE-ST) outside Glasgow. This 12m2 wall recycled over 1.5 tonnes of waste, saving over 300kg of carbon emissions compared to if a traditional clay brick had been used.
“We are delighted that a leading client and global architect has designed and built a pavilion within the Green Zone at COP28 using the K-BRIQ, giving us an increasingly higher platform to promote our sustainable product and unique production approach. Heriot Watt University has also built a striking K-BRIQ wall on its new Dubai campus using the product, a spin-out company from the University. This is a permanent feature, but will be part of the COP28 exhibition.
“Further to this, leading real estate player, CBRE has used the K-BRIQ in some striking room dividers within one of its offices, and there are various hospitality project interiors that are showcasing the K-BRIQ within striking counter and wall designs, including the Gail’s Bakery chain. 50m2 of K-BRIQs have also been used on the lower course of a large industrial building in East Lothian, which has been in place for over 2 years.
“Kenoteq possesses a strong pipeline of projects across the UK where the K-BRIQ has been specified. These will begin on-site this year, so we look forward to publicising these as they begin to take shape.”
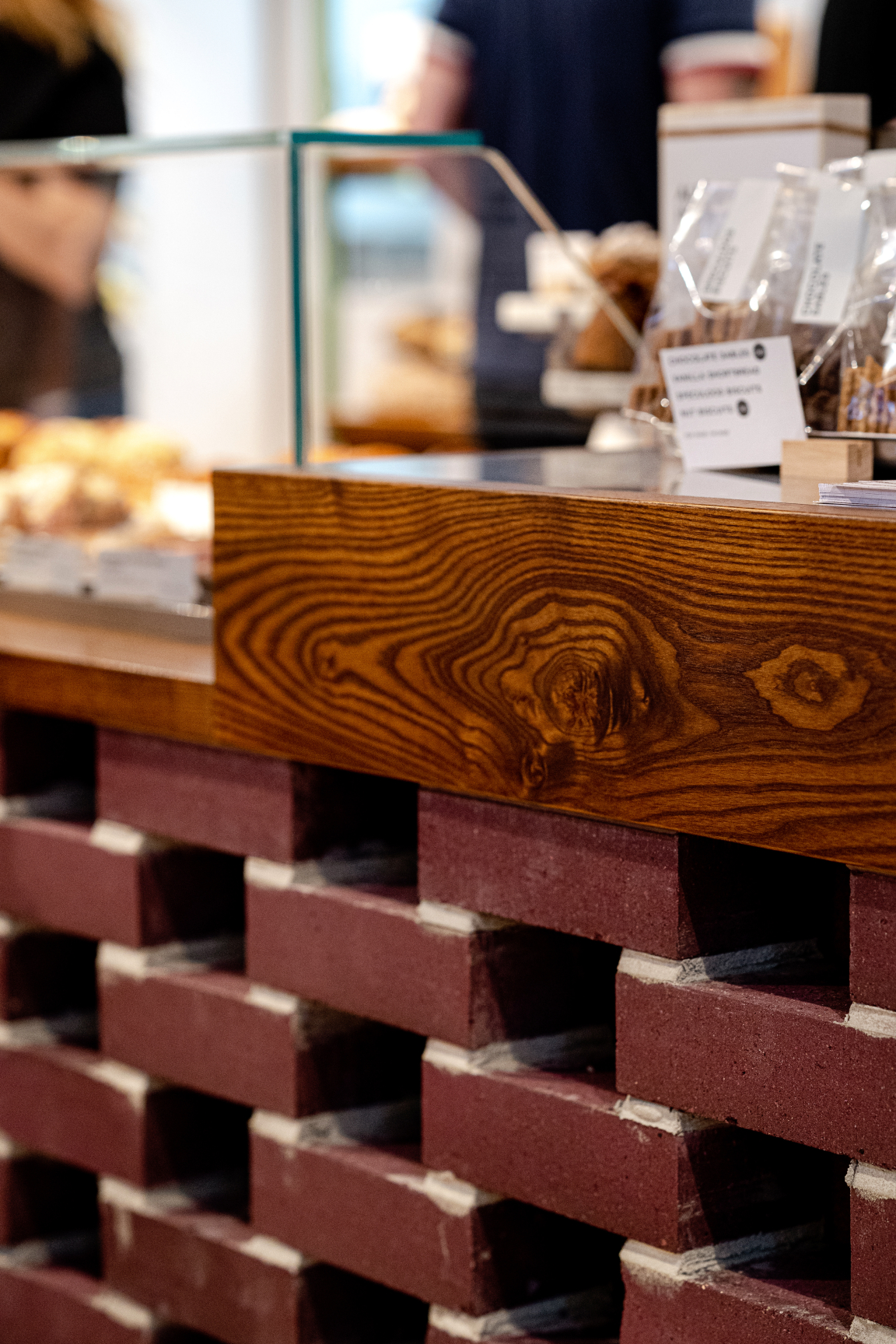
Gails Bakery, Manchester
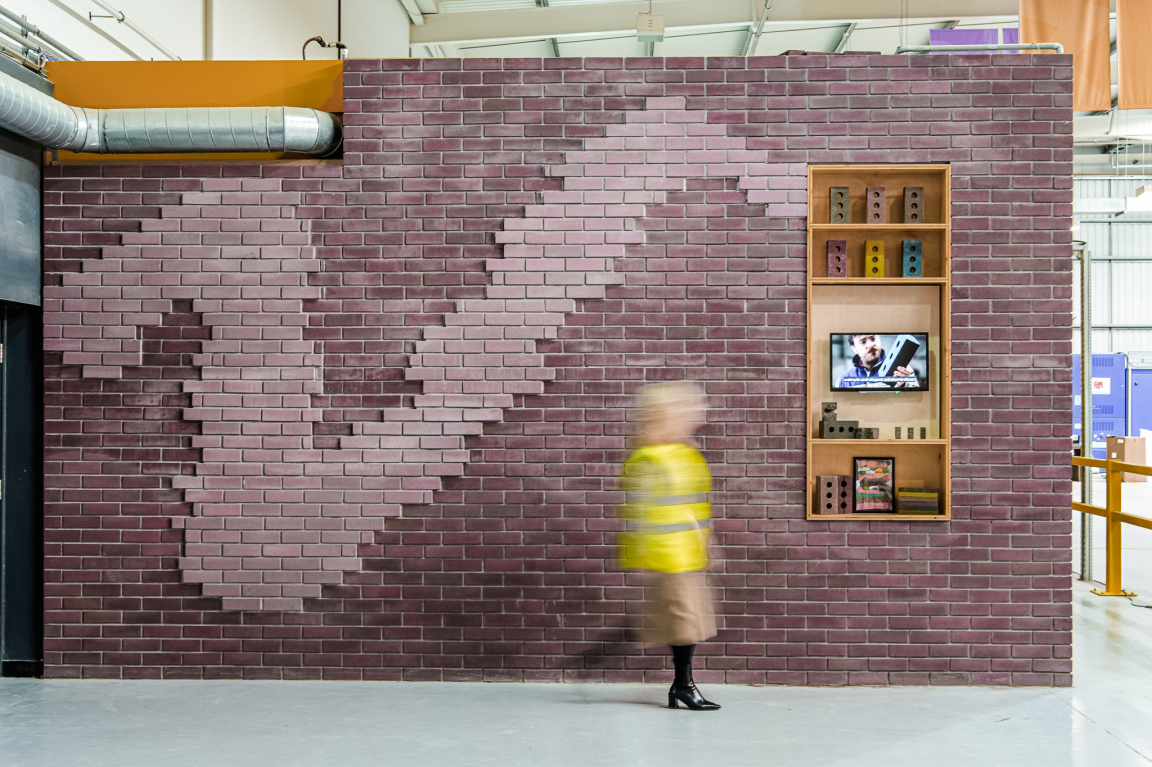
COP26 - BE-ST Demo Wall
How does K-BRIQ compare to a regular construction brick?
“Technically the K-BRIQ is highly competitive to a traditional clay or concrete brick – this is where the years of research and development have been focused. However, the K-BRIQ’s differentiators are its ultra low embodied carbon, its recycled waste content and the fact that it can be recycled into new building products, providing a closed loop circular economy model to the built environment.
“The K-BRIQ is a speciality brick, ideally suited to projects with net zero targets, clients with a strong ESG focus or a drive to lower embodied carbon in their builds, like the Scottish Learning Easte Investment Programme (LEIP) - which sets embodied carbon targets of 600kg CO2e/m2.
“The City of London Corporation also now has a focus on tackling the assessment of whole lifecycle carbon for all new major projects including minor refurbishment, major refurbishment, extension and new build, with ‘material consideration in the determination of planning applications’.”
What relevant certifications does the product hold that built environment professionals should know about?
“The K-BRIQ has recently completed its final certification testing with the British Board of Agrement (BBA) with final certification expected by March/April 2024. At which point, the product can be formally used in exterior build programmes. However, the product is being specified currently and can also be procured now for use in interior projects where certification is not necessary. NHBC certification and CE marketing will follow on the back of the BBA certification. As a non load-bearing facing product for the interiors market, there are no formal certifications required for this application."
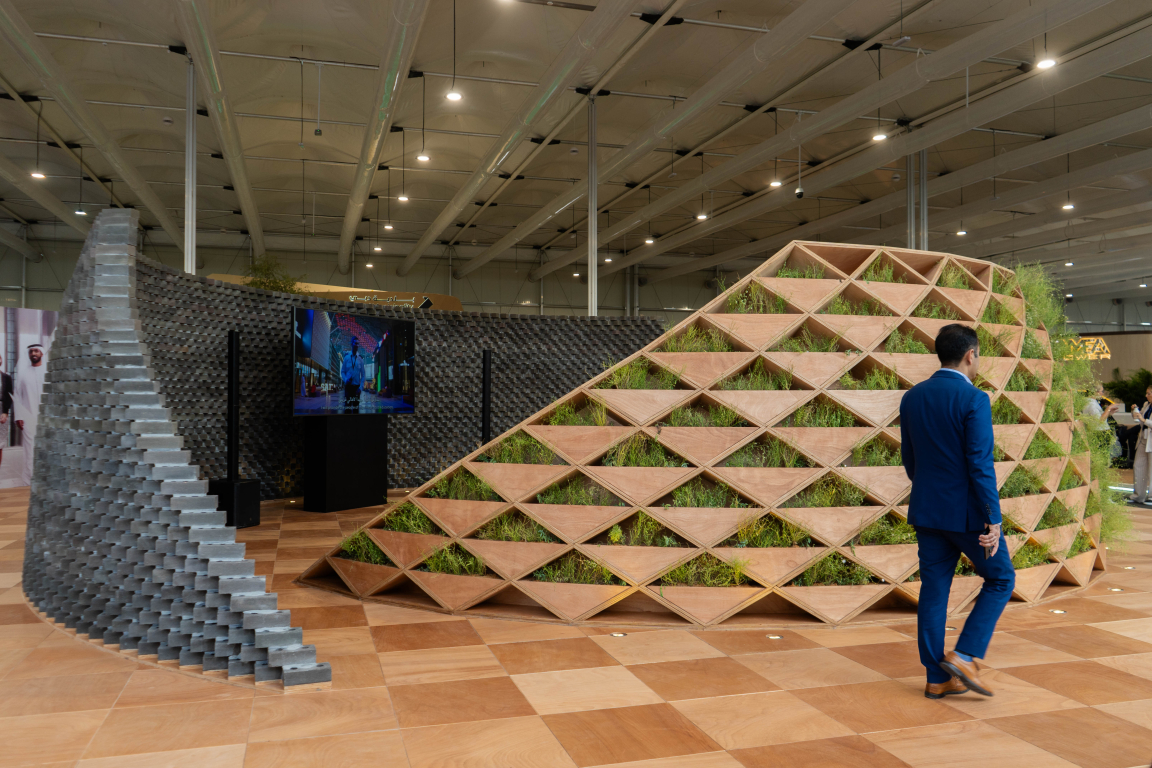
Holding Pavillion, Dubai
Are you developing any new products at the moment?
“Whilst we have a K-SLIP brickslip product available currently for use in interiors, we are focused on testing this on various façade fixing systems in order to certify its use in a suitable system later in 2024. This would provide the façade market and offsite manufacturers with a sustainable, lightweight, quick and efficient way to clad their facades.
“We also hope to bring out flooring and paving options in the very near future. Our production system allows us flexibility in terms of shape and colour, so we have a product roadmap for other iterations of products using the K-BRIQ’s overall composition, which will see other products like blocks and roof tiles coming to market in the future.”
What’s next for Kenoteq?
“2024 will be a landmark year for Kenoteq as the K-BRIQ heads into commercial manufacture and into build projects - within the pipeline of projects we have built up. We cannot wait to showcase the product across these pioneering projects and build on client and specifier interest, helping to drive down carbon emissions in the built environment, and support green jobs and local supply chains in the process.
“As demand grows, we will look to implement our scaling model, setting up production facilities in partnership with waste management companies across the UK and internationally. There is so much interest in our product and business model, it will be great to operate at full capacity and grow.”