Nomique's Blue Finn sustainable stools repurpose hospital waste.
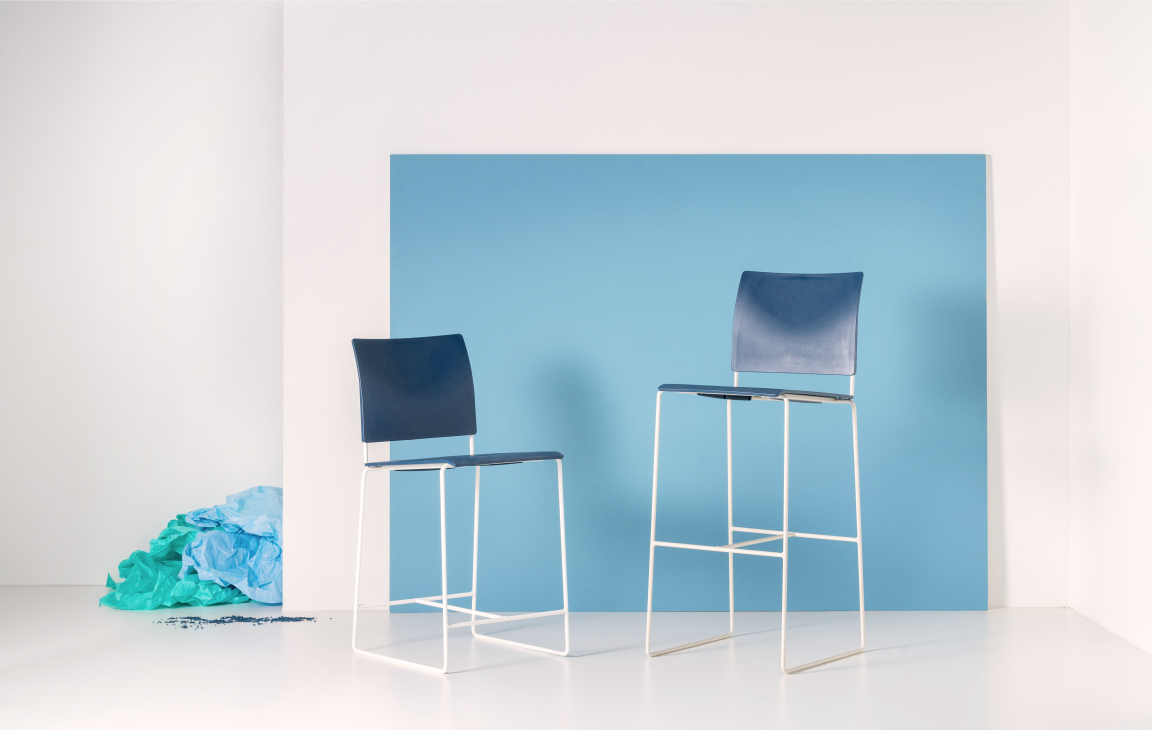
The supply of sterile instruments for operating theatres is a top priority for hospitals. To keep these instruments sterile, they are covered with wrapping material, in many cases: Bluewrap. And although this waste material cannot be prevented, reducing waste is an important objective for every hospital.
The raw material
Bluewrap consists of 100% polypropylene, so-called meltblown and spunbond homopolypropylene. Bluewrap does not look like plastic but rather like a fibrous material. Nevertheless, polypropylene is easy to recycle. However, it does require a different recycling process than, for example, the recycling of PET bottles. Bluewrap is used, discarded and then collected in cooperation with a waste collector.
Creating value
Every year, no less than 40,000 kg of Bluewrap is thrown away. A shame! That is the opinion of the hospitals. And Nomique too. That's why they joined forces a few months ago to find a solution for this residual material.
Complete supply chain
Nomique doesn't do this alone. It works together with its knowledge and chain partners - from hospitals to waste collection and processing, cleaning, compounding and injection moulding.
The process
- Bluewrap is used, separated from other waste, collected and bound into packages.
- These packages are collected by the waste processors and taken to a sheltered workshop in Zwolle.
- At the social workshop, the packages are prepared for processing, the tape and any labels are removed manually because (in this process) it is not possible to recycle it.
- Bluewrap is recycled in batches of 2000 kg. From these 2000 kg, Nomique can make about 1350 chairs. About 1.6 kg Bluewrap is used per chair.
- After removal of the tape, the clean and 100% polypropylene cloths are agglomerated.
- During the agglomeration process the Bluewrap is grinded and heated until a spherical agglomerate is formed. This agglomerate looks a bit like popcorn.
- This brittle material is then upcycled into granules. This is done using a twin screw extruder. The brittle material is melted under pressure, purified and degassed of any volatile substances.
- Then additives are added to improve the impact resistance and make the granulate more fluid in the injection moulding process.
- The granulate is packed in octabins (= an octagonal sleeve with bottom + lid that is often used in the plastic industry) and transported to Timmerije.
- The granulate is injected into a mould so that the seat and back of the chair are created.
- The chair is then assembled in Wijchen and is ready for shipment to customers.
With Blue Finn, the possibilities span multifunctionality, comfort, strength and durability. This product truly displays upcycling at its finest, with 100% reuse achieved. And after use, the stools can be handed back to Nomique to be recycled once again.
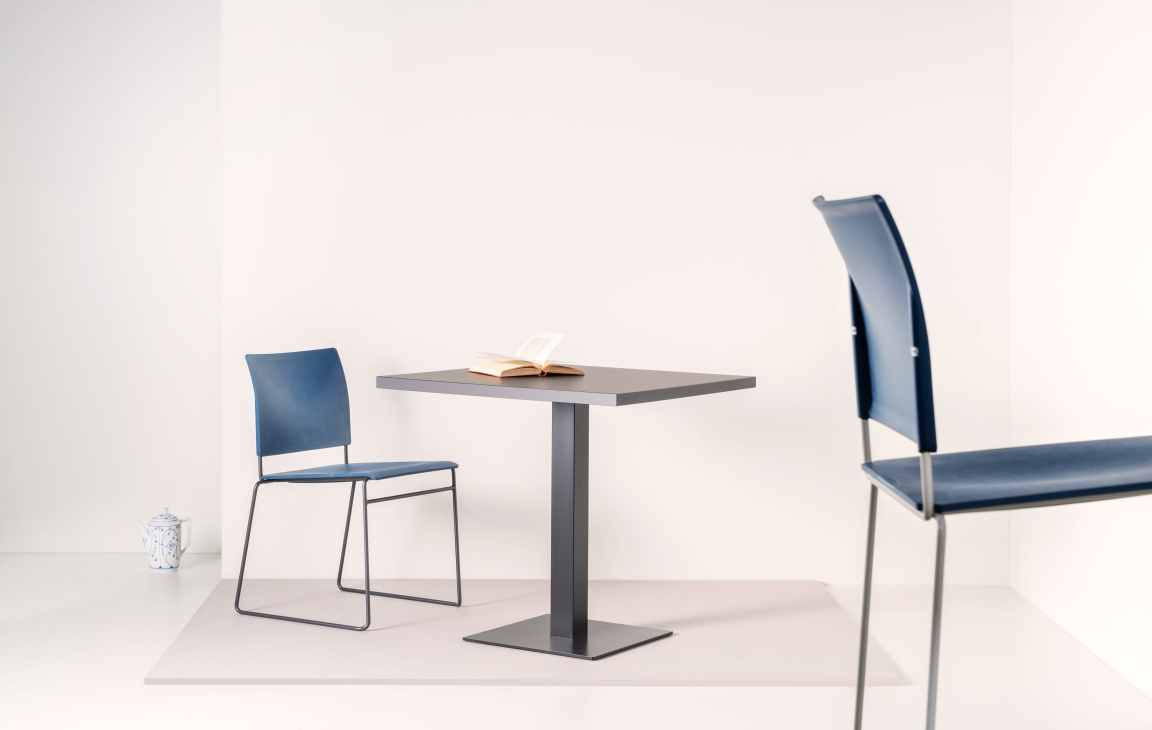