Anne Asensio & Arthur Mamou-Mani on Aurora at the Design Museum during COP26.
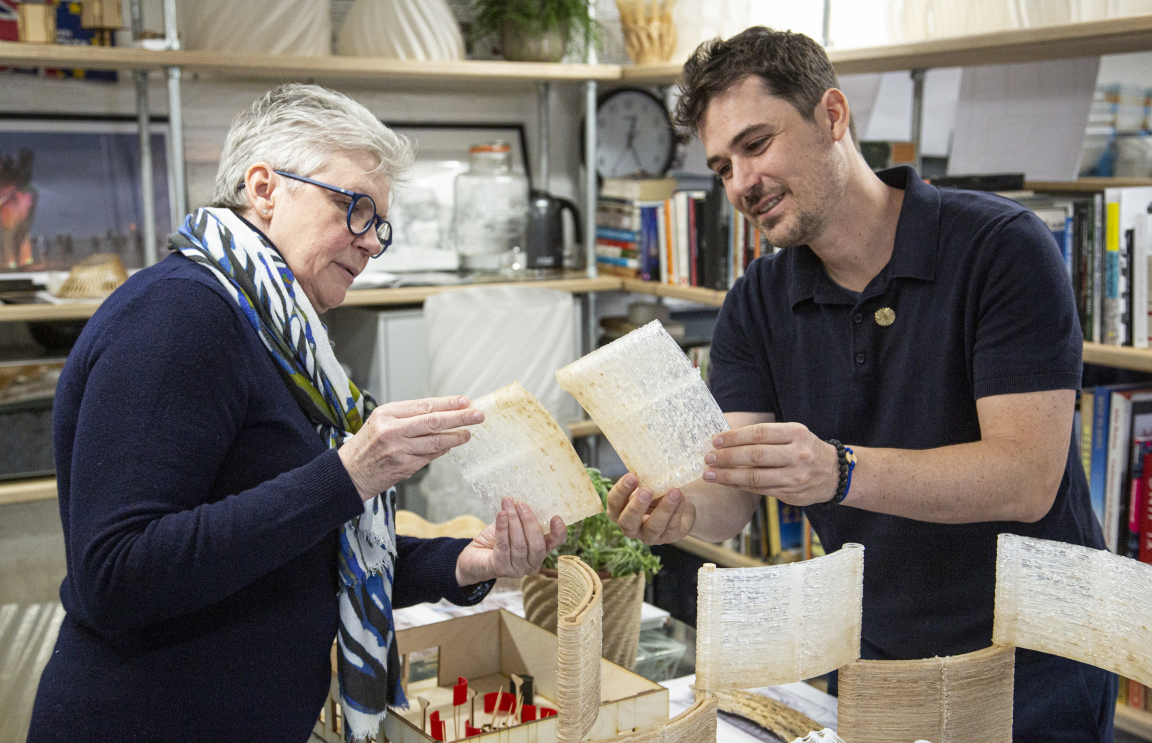
Credit: Dassault Systèmes
As the world's leaders meet in Glasgow for the COP26 summit, the design industry is doing what it does best: innovating, utilising byproducts and conjuring up objects of true beauty.
Over at the Design Museum, a series of exhibits mirroring the wider conversations taking place around climate change and circular economy are in full swing. Greeting visitors to Waste Age: What can design do? is Aurora - an interactive installation by Mamou-Mani Architects in collaboration with Dassault Systèmes Design Studio.
Inspired by Upstream Thinking - a design approach that prioritises regeneration - the showstopping piece explores how we can achieve a more sustainable approach to life in the future: a world in which design, science and industry converge to ensure that everything we create and manufacture involves sustainability.
We discussed the creative concept and making process of Aurora in more detail with architect Arthur Mamou-Mani and Dassault Systèmes' Anne Asensio. Here's what they had to say...
Can you give us an overview of your Aurora installation at the Design Museum?
Arthur Mamou-Mani: "Aurora is a 3D-printed modular installation made of 300 modules that we created in collaboration with the Dassault Systemes Design Studio located in the Atrium of the London Design Museum, and part of the Waste Age exhibition. It has been printed from bioplastic polylactic acid (PLA), a non-toxic thermoplastic derived from sugarcane. Aurora is actually an illustration of how design, science and industry can come together and enable us to produce more sustainably.
"On the upper mezzanine of the atrium, visitors can discover the virtues of PLA – compared to ABS, a petroleum-derived thermoplastic. Both a 3D-printer and plastic crusher are also showcased so visitors can understand how the modules are being crushed, melted and reformed, as PLA can be recycled and printed again in a continuous loop."
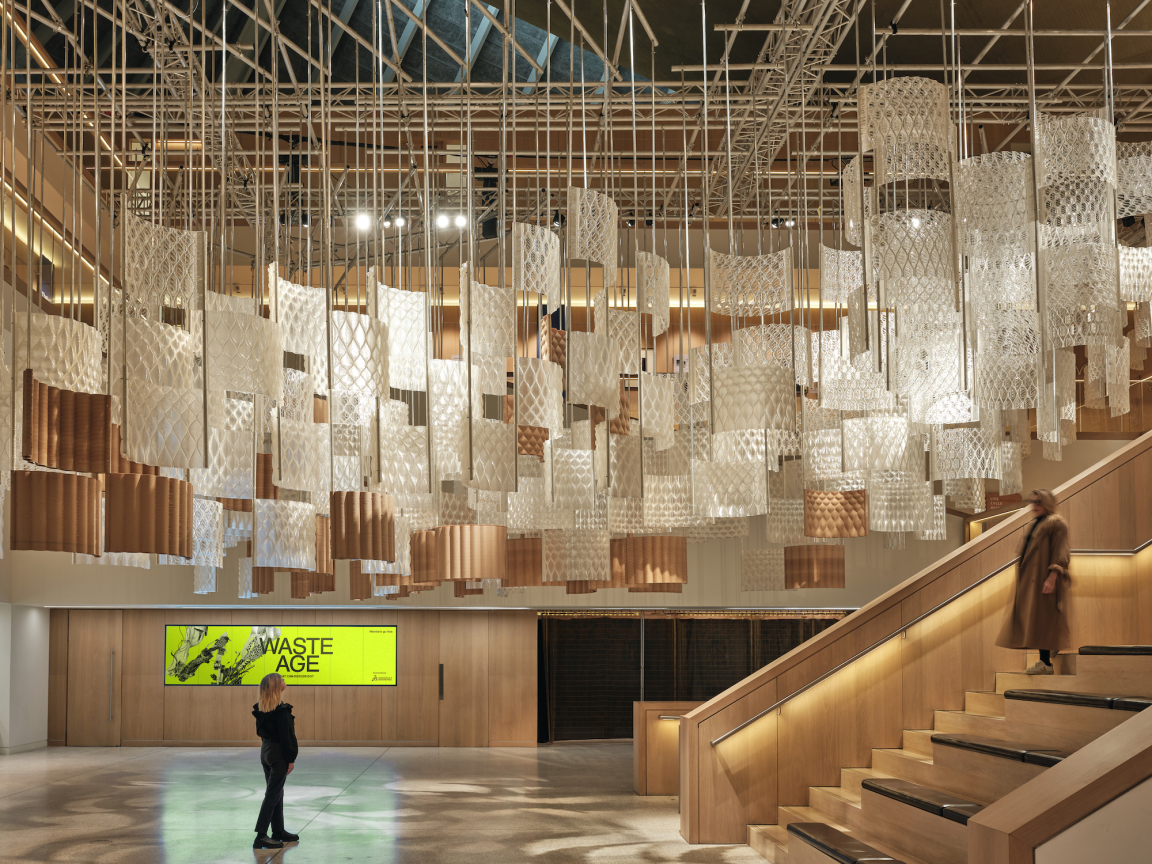
Credit: Felix Speller
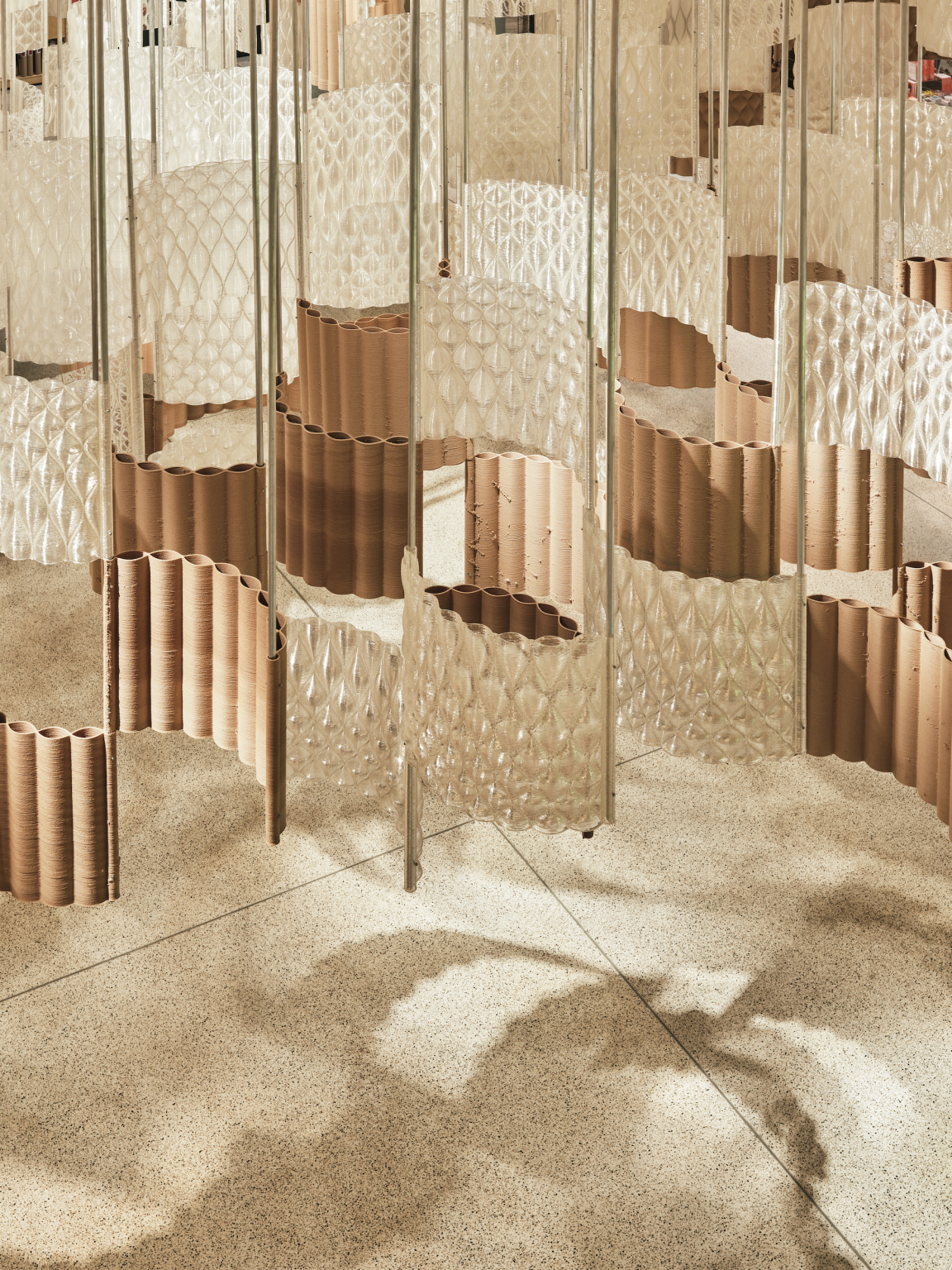
Credit: Felix Speller
So, the piece demonstrates the principles of circular architecture?
Anne Asensio: "Indeed. Aurora has become more than simply a piece of art and really questions the principle of circular economy. By questioning every aspect of its production and lifecycle, from a detailed assessment of the environmental impact of the material through to the possibilities for disassembly and reuse, we wanted to take the audience along on a journey that questions how we may design and create habitats in the future and how we can reach circular economy. What we want to do is embrace the circular design principles where we are designing with details in mind.
Regeneration involves selecting the right materials that have an opportunity to be regenerated, reused, recycled, repurposed, and redesigned.
"If you want to design for regeneration you first need to choose the right material by testing structural capacity. Secondly, assembly and disassembly. When you assemble a design, you may think about its disassembly – whether it’s going to be very easy to take apart and recycle within the system or reuse or repurpose. This is the power of the virtual. The result is that designers will have full traceability of the final impact - that’s what we call regeneration and that’s how we can reach a possible circular economy. In this case, PLA was selected as it can be recycled and printed again in a continuous loop."
How does the piece reflect on, or respond to, the global pandemic?
Arthur Mamou-Mani: "The global pandemic has really shown how dependent we are on factories that are outside of our country, and how reliant we are on very polluting modes of transportation for materials.
"I'm quite excited to show how things can be grown and made locally; grown because material can be grown. It doesn't have to be mined. And then, how these materials can be made locally in many factories with 3D printers - eradicating the need for travel. I think this is something very positive to have come out of the pandemic. We were 3D printing the PPE, the protective equipment for the hospitals, and that really opened my eyes."
Aurora is exhibited alongside the Waste Age exhibition, which coincides with COP26. What do you hope will come out of these events in terms of a more sustainable future?
Anne Asensio: "As a designer, I strongly believe that design has a very important place within all the 17 sustainable goals. By supporting the creative industry we can shift our surroundings, but more importantly, shift our behaviours.
COP26 is not just about policy making, it's about embracing circular design and circular economy principles, putting design at the core and enabling and empowering designers and architects.
You designed Aurora virtually - can you talk us through the creative process?
Anne Asensio: "I don't think creativity follows a process. It's more iterative, you do something, you learn from it, and then you think about something else. So we should not make the mistake of thinking that because our platform is virtual it ends up becoming something very regulated.
"The virtual space is more like an environment to play, test, imagine possibilities. It’s not narrowing down quickly to create a process to be more efficient. We really want to reinvent a new environment, outside of the box, that can be sustainable by the fact that it properly proposes a better circular economy.
"Arthur is someone who is already very familiar with technology. So he knows how to create a dialectic with technology. He already had this habit, but his process is really what's creative. With the design studio team, what we wanted to do is to leave him as the conductor and we were simply providing him the best conditions for expressing Aurora. So, the creative process, if we can call it that, was not affected, it was just amplified. We wanted to empower Arthur.
"One key element of the project was that it required teamwork. It needed a collaborative effort. Every time you get and tackle a very complex situation, you need to be more than just one person. So, the challenge moves from being creative to understanding each other and coming up with some challenging ideas that may change Arthur's thoughts. The process was an iterative one. We put in more staff, more indicators, more creativity, or, from the design studio team, experts that are super experts in particular areas of the 3D experience platform - that combination is how we were able to make this happen.
"But perhaps most important with this is the promise. I think the reality is that we have put together a new way of doing architecture, rethinking architecture, not from a big mass production of dwellings, but maybe something more close to the scale of human beings. Something closer to our real needs without compromising on the quality of life."
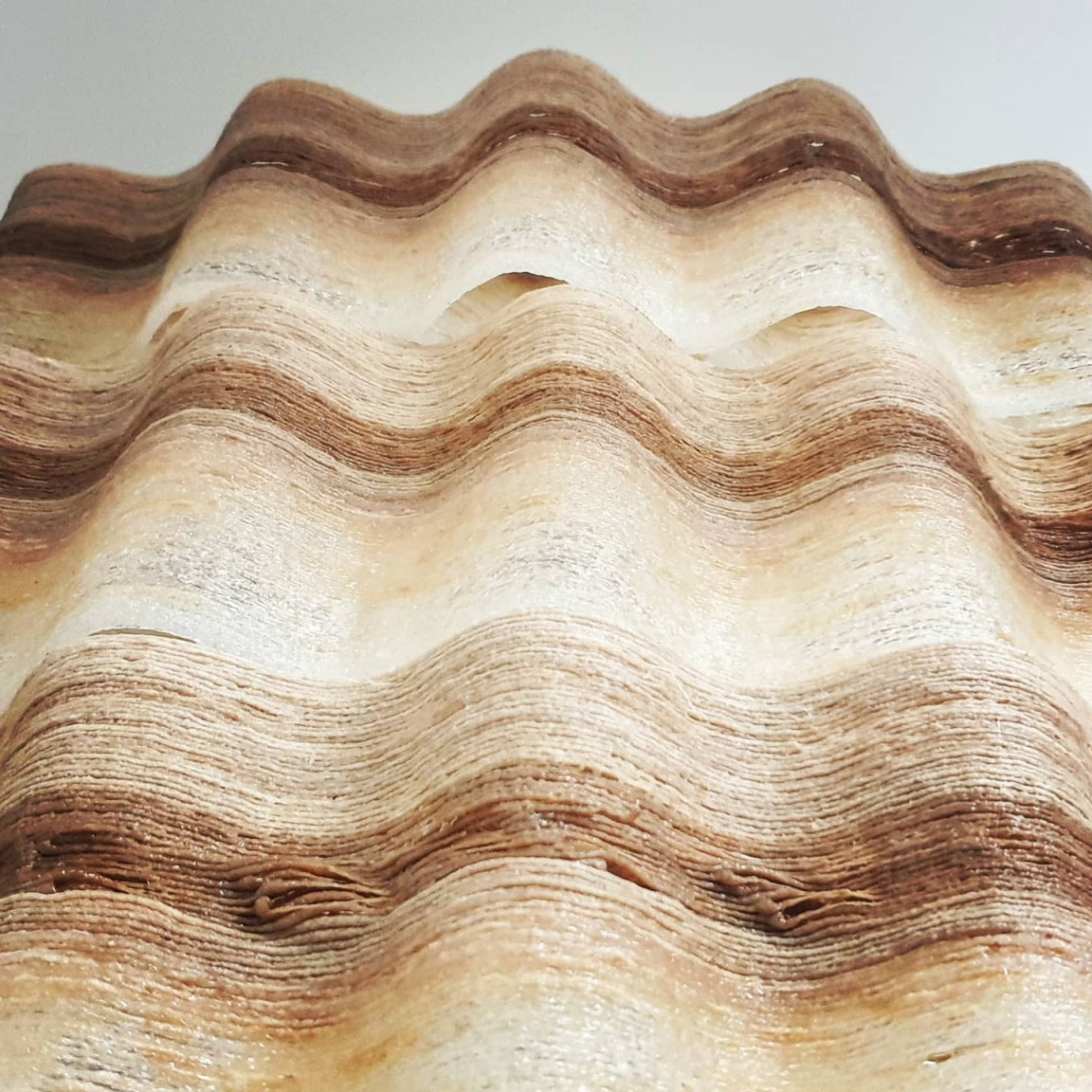
Credit: Mathieu Leborgne
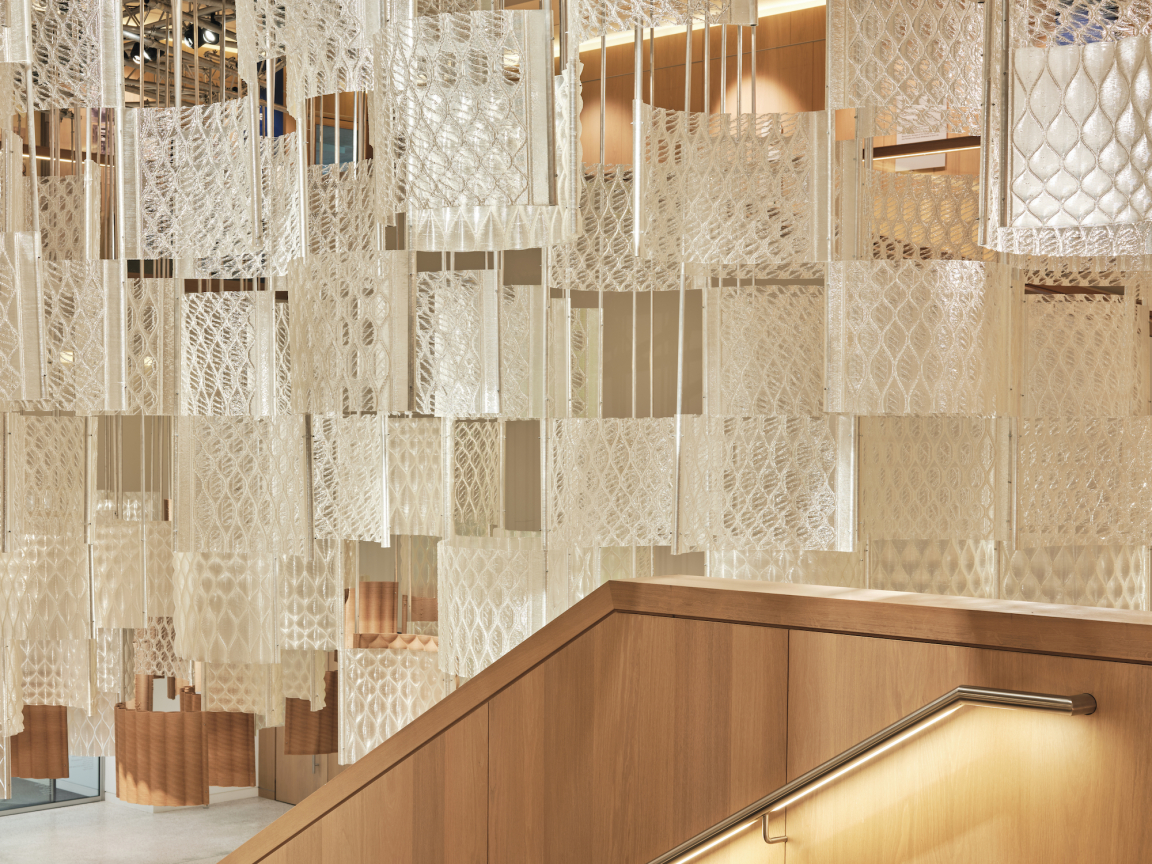
Credit: Felix Speller
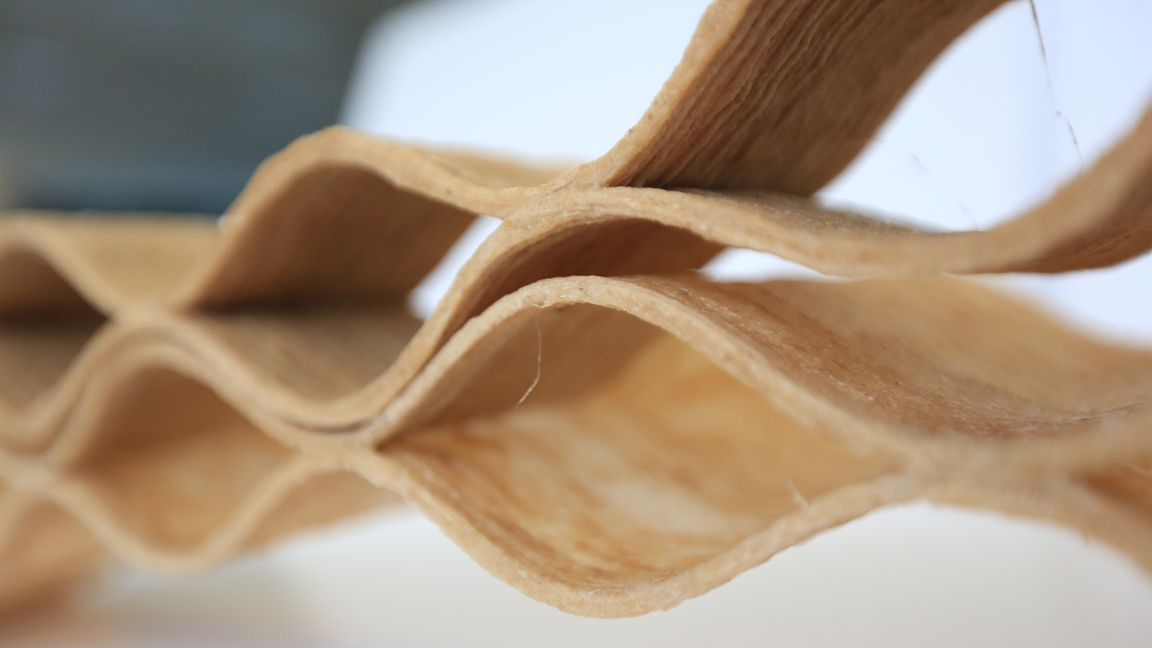
Credit: Mathieu Leborgne
How is your technology helping architects and designers to make more sustainable choices in their work?
Anne Asensio: "The 3D platform is basically the cradle for collaboration. The capacity of the platform is to virtualise any idea - transforming it into what we call the 'virtual twin'. Basically a three dimensional, virtual representation of the design, whatever it is. In the past, 3D was really to secure the design of a given object. However, today, creating a three dimensional space allows you to design the context too.
"This was the case for Aurora, the installation was designed for the studio in Milano. So we basically had to design the surroundings first. We designed the entire architectural studio, and then we placed the Aurora installation.
"When you take the context and constraints into consideration, you can play around with the 3D, you can have multiple scenarios and visualise it - just like in real life. In this way, the user can make very quick decisions.
"On top of the virtual twin, or the three-dimensional representation of the design, external conditions can be placed. So, that could be airflow, sound, light, etc - all very important elements to actually experience via simulation in advance, as they may happen in the real world.
"We also have the ability, because we have a three-dimensional model, to imagine the entire life of of it, by thinking of its assembly, disassembly, reuse or recycling, repurposing or reinstalling...
"So, beyond iteration, this 3D process allows you to be very sustainable by managing the full life cycle of the installation.
"We provide architects and designers with a virtual environment; the best metaphor for what we provide is that when architects or designers are working in a workshop, they are working and bringing different expertise, different knowledge, different ways of doing, and it's really experimental. It's just by providing all those capacities through our platform, they can resolve an issue more efficiently.
"We can also extend the level of information offered to include where a material comes from, where it’s being extracted, how it’s being extracted, and its inner quality. We can go to the molecular level and we can actually test the way the molecular level evolves with a reprinting movement. Where you have print and reprint, you can check if the molecular level is the same or how much you have lost on the plasticity of the material in the process.
"You can test every step of the way, you can track logistics, you can track the amount of water that has been used in the whole process. It's really expanding the capacity to make decisions at the scale of the challenges that architects and designers have to tackle."
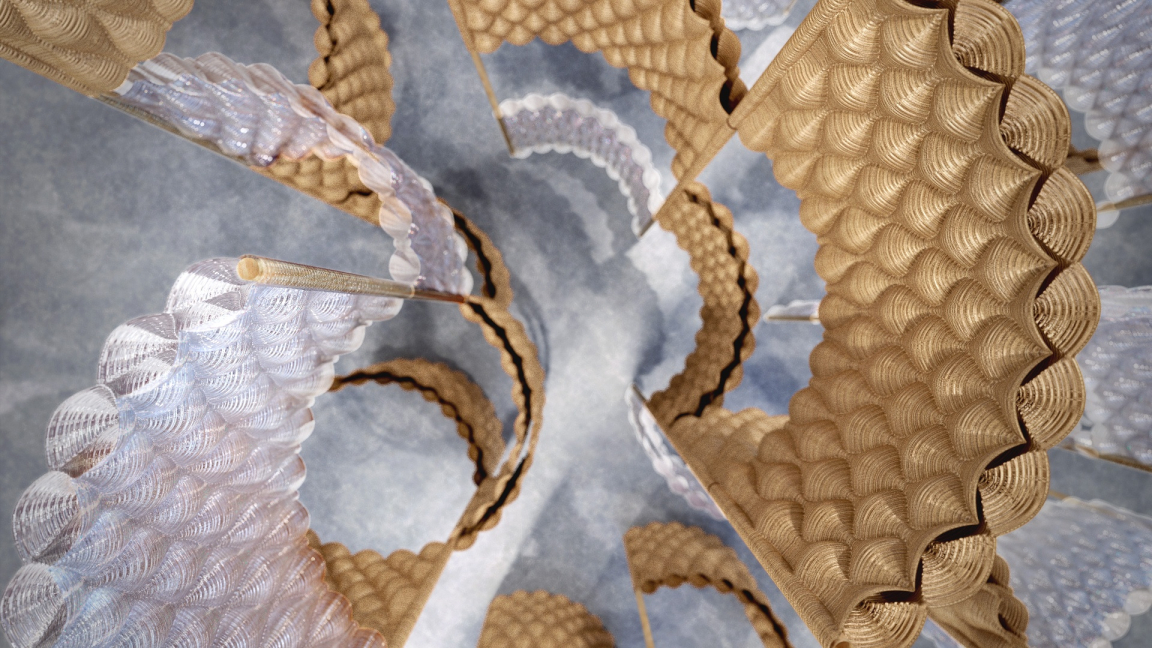
Credit: Dassault Systèmes
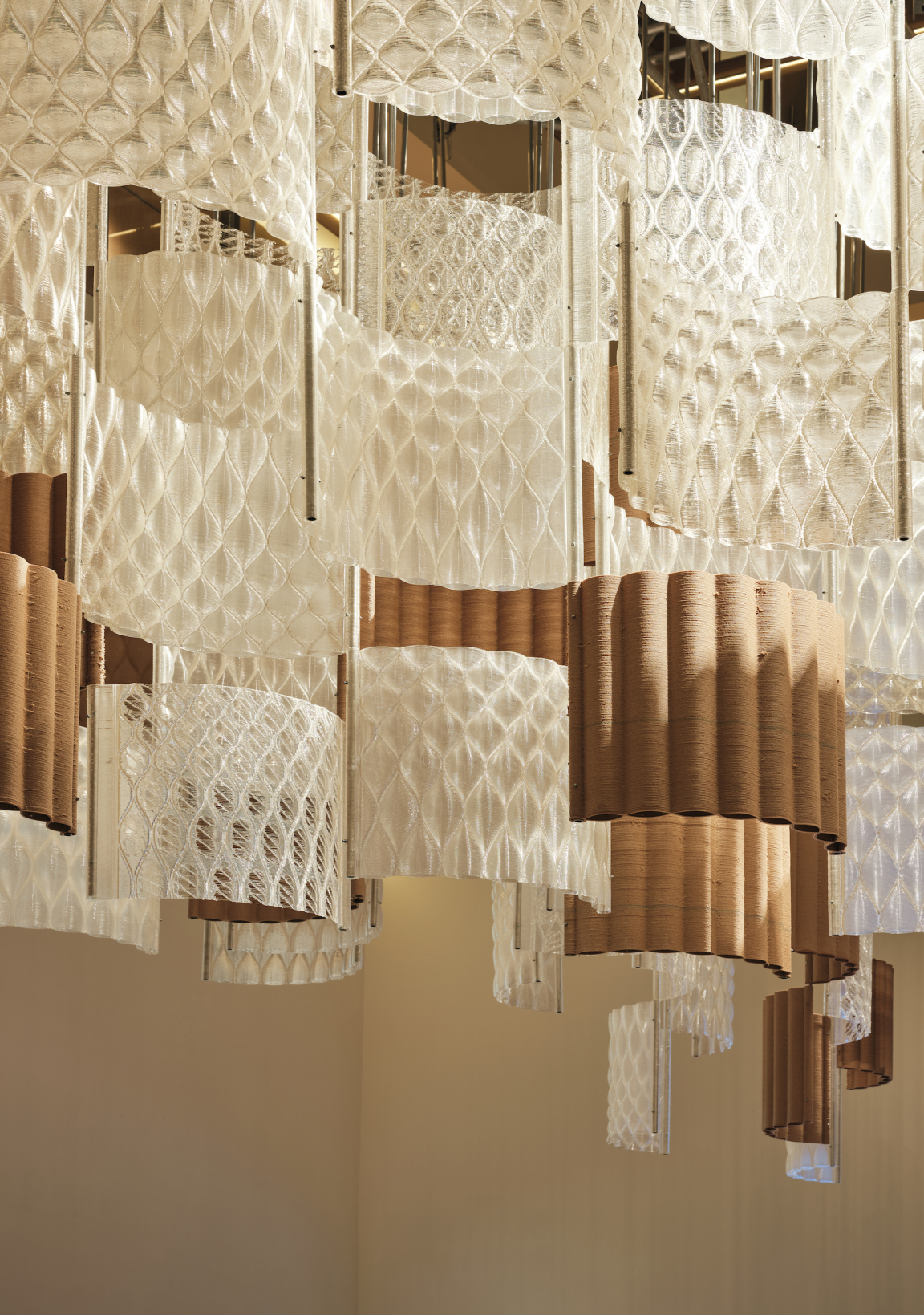
Credit: Felix Speller
As a champion of sustainable materials, are there any particular makers that should be on our radar right now?
Arthur Mamou-Mani: "In terms of making, I would say Nassia (Inglessis) from Studio Ini is on my radar. In terms of sustainability, I would say Chris Precht from Studio Precht, creates the most amazing modular designs and eco perimetric structure."
What’s your favourite material to work with?
Arthur Mamou-Mani: "Of course polylactic acid is my favourite material. It's a bioplastic that comes from fermented sugars. I've been working on it with Conifera, Mellifera and more recently Aurora. The trio of projects explore this material for architectural purposes, and look at how it can be grown, as well as composted or biodegraded, and also its aesthetic, the kind of beautiful patterns that can be created from the 3D printer parametrically."
What are you working on next?
Arthur Mamou-Mani: "A tower made from reclaimed wood in Bali, an echo home in East London, a chandelier, 3D printed in Scotland, using PLA mixed with a fireproofing, which will probably be one of the first PLA fireproofed installations in the world. We're also working on a very exciting retail facade project.
"I'm also excited to say that we received investments for Fab.Pub, our fabrication company to have many Fab.Pubs around the world. That's something very close to my heart because it means that we're going to empower many communities to 3D print things, and that is a really beautiful thing, to help spread our technology and our materials for good."