Elizabeth Bridges & Garrett Benisch of Bioforcetech on transforming feedstock, changing behaviour & world domination.
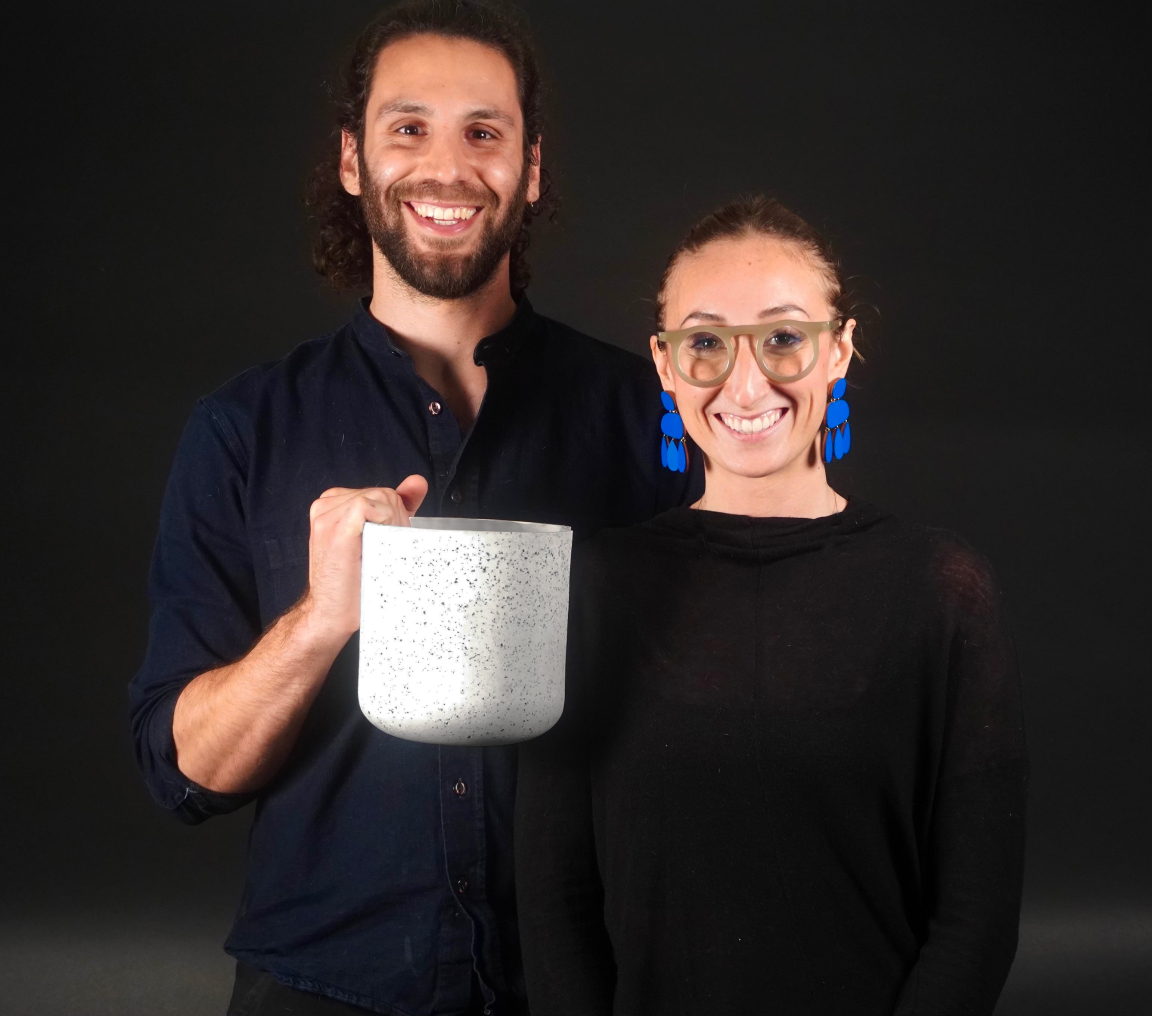
Image courtesy of Bioforcetech
Ahead of the opening of From The Ground Up - the first exhibition of biomaterials and sustainable alternatives to be held in the North of England at Material Source Studio - we were keen to catch up with some of our contributors one-on-one.
First up are Elizabeth Bridges & Garrett Benisch of Bioforcetech, a fascinating Italy/California based technology producer with a ground-breaking system that transforms any organic feedstock into a fixed carbon material.
Firstly, can you please introduce us to Bioforcetech? And the OurCarbon project?
"Gladly! Bioforcetech is an Italy/California based technology producer with a really amazing system that transforms any organic feedstock into a fixed carbon material. The system can work with many different organic materials as its feedstock input, but Bioforcetech has started by working with one of the most inevitable waste materials we produce; biosolids, the solid residuals from wastewater treatment.
"The processing of this material through this technology is so sustainable that every one tonne of it we produce prevents ten tonnes of CO2e from emitting into the atmosphere; the equivalent of taking two cars off the road for a year. Our closest installation here in California produces that much material every day, so it really adds up.
"We’ve called this new material ‘OurCarbon,’ and have been working to share its amazing new CO2 stopping story while finding new uses for the material in global industries that expand its impact."
How did the company come about? And what led you to being a part of it?
"Bioforcetech was born out of a conversation between our founder, Dario Presezzi, and his father at the dinner table one night in Vimercate, Italy. Through that meal, Dario realised the sheer volume of organic material that was being wasted every day and was so moved by this discovery that he set out to shift how we process ‘waste.’ Ten years from its founding and now Bioforcetech is making this change at full scale!
"We entered the scene last summer, after Garrett had just finished a thesis focused on trying to shift society’s views on disgust, part of which involved him making a black ink out of carbonised biosolids himself. I was finishing the design phase on an experiential Climate Change exhibit for a Smithsonian museum, and we had just formalised our professional collaboration by taking on our first client for our design collective, Sum Studio. We were brought on as a team to give this material an identity and communicate its story to the world while developing it to be utilised."
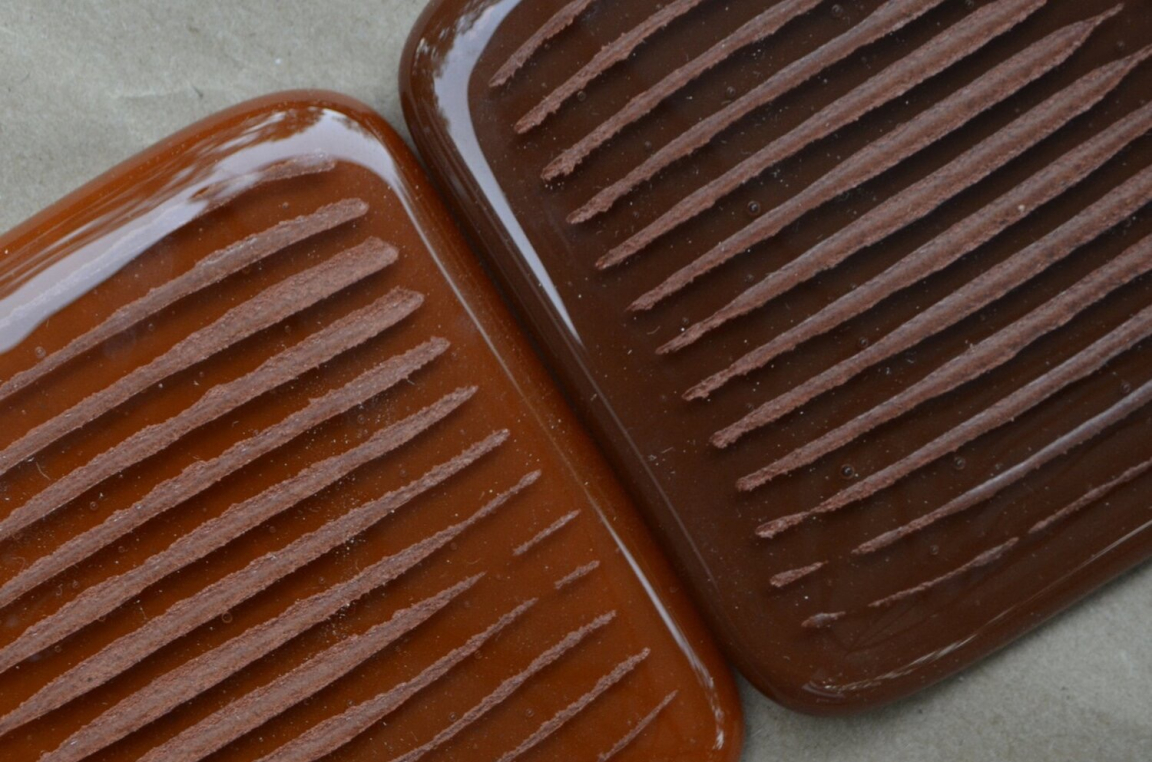
OurCarbon Glass - Aaron Ethan Green
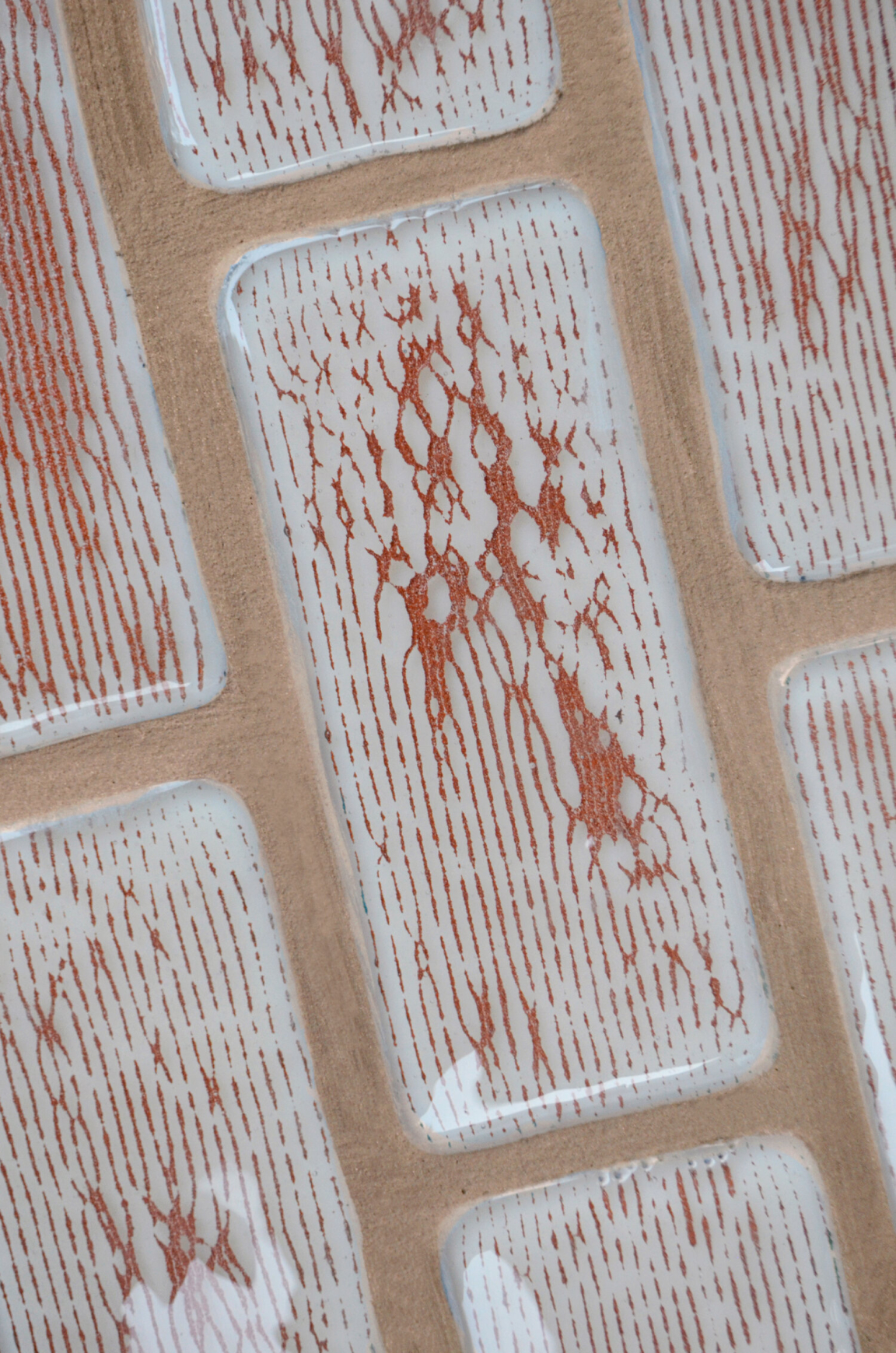
OurCarbon Glass - Aaron Ethan Green
What does a typical day in the life of your job look like?
"As a small team taking on big projects, our days at BFT vary from hour to hour. Morning calls range from sustainability heads at large fashion brands to industry experts deep in a supply chain that are testing OurCarbon in a new application. Then I might get to work on producing material samples for groups like Material Source while listening in on a presentation on regulations for landfills while Elizabeth might be doing research on specific dye techniques or working on establishing carbon credits for the emissions prevented during the creation of the material. It’s a really broad scope and we’re involved at every stage from regulation and implementation to marketing and communication."
What types of companies does Bioforcetech support?
"OurCarbon has definitely piqued the interest of large, established companies which could create a huge impact very quickly by integrating the material into their supply chains.
"We also take every chance we get to work with small businesses and to collaborate with other sustainable material producers to establish completely new supply chains. For example, our recent exhibit called What A Waste at Dutch Design Week ‘21 showcased the possibilities of OurCarbon through the work of seven different independent designers. Plus, the entire exhibit was made of Honext, these amazing new panels made from cellulose waste, that were painted with OurCarbon tinted paint. These kinds of endeavours set an example of how to collaborate with designers and how to showcase a product with a light footprint."
Can you briefly talk us through how your BioDryer and Pyrolysis system works?
"Of course, the technology behind OurCarbon truly is just as innovative as the material itself. Since we work with such wet waste streams, the first task in making the material workable is removing the excess moisture. Dario’s background in Biotechnology led him to really innovate on drying processes by taking advantage of some key bacteria already present in the wet biomass. Drying wet organics is typically quite an energy intensive process, often done by blasting the material with hot air generated by natural gas.
"Instead of burning external fuel, Bioforcetech’s BioDryer uses bacteria already present in the feedstock to dry out the material. As the BioDryer circulates air throughout the biomass inside and creates favourable conditions for those bacteria to thrive, they throw off heat that in turn evaporates almost all of the water. It’s really simple, yet really innovative! The dry material is then ready to be transformed into OurCarbon through the second step; pyrolysis.
"Pyrolysis is the decomposition of an organic material achieved by heating it in the absence of oxygen. When this process occurs, two substances are generated: a hydrocarbon gas and a biochar. In our system this gas is utilised right away as a fuel source to power the pyrolysis process continuously. There’s even enough energy generated to share back to the BioDryer to finish off the drying process started by the bacteria! This energy generated during the pyrolysis process is what allows the whole system to power itself as it runs.
"As for the solid biochar, the lack of oxygen in the heated system forces the material’s carbon to connect in a very tight bond instead of linking to oxygen and forming CO2. The process makes the carbon bond so tightly that it cannot be broken or emit as greenhouse gas for thousands of years. So now this organic material has transformed into a stable carbon material, and all of the contaminants that were a regulatory risk for the biosolids have been destroyed as well (think microplastics, pharmaceuticals, and even ‘forever chemicals’ like PFAS all destroyed!). It’s really a win-win-win from an energy, regulatory, and output perspective."
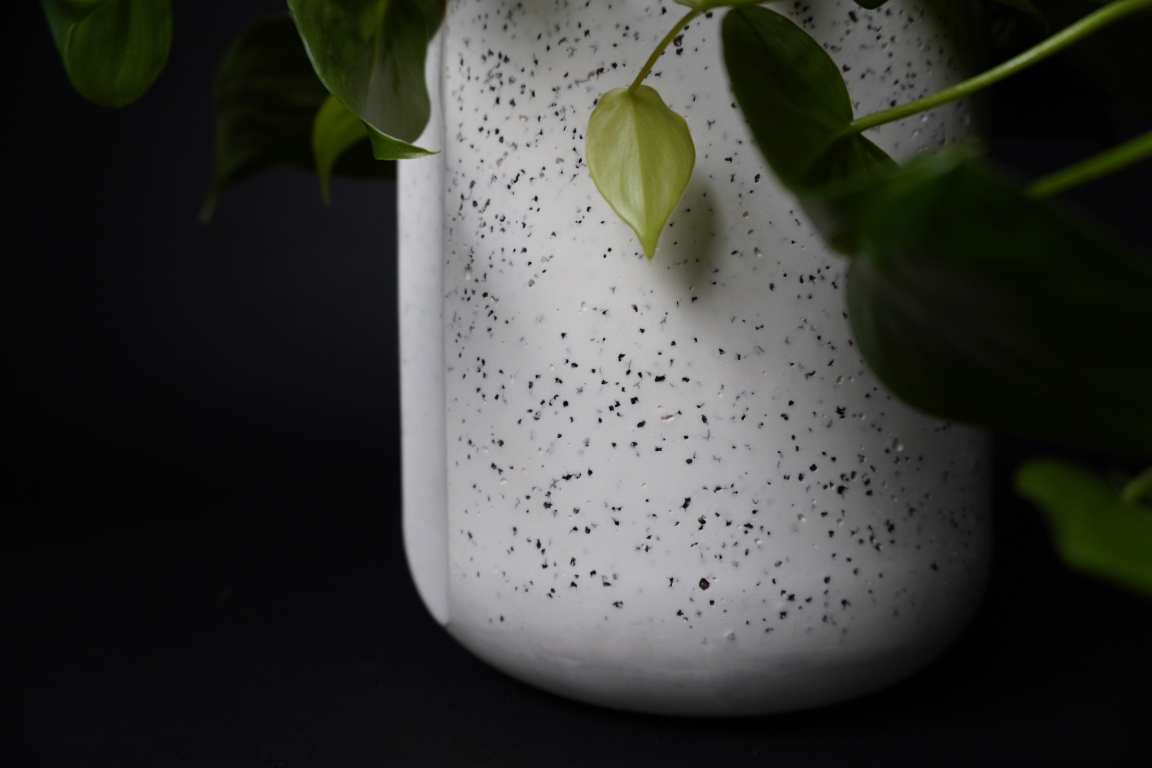
OurCarbon Porcelain
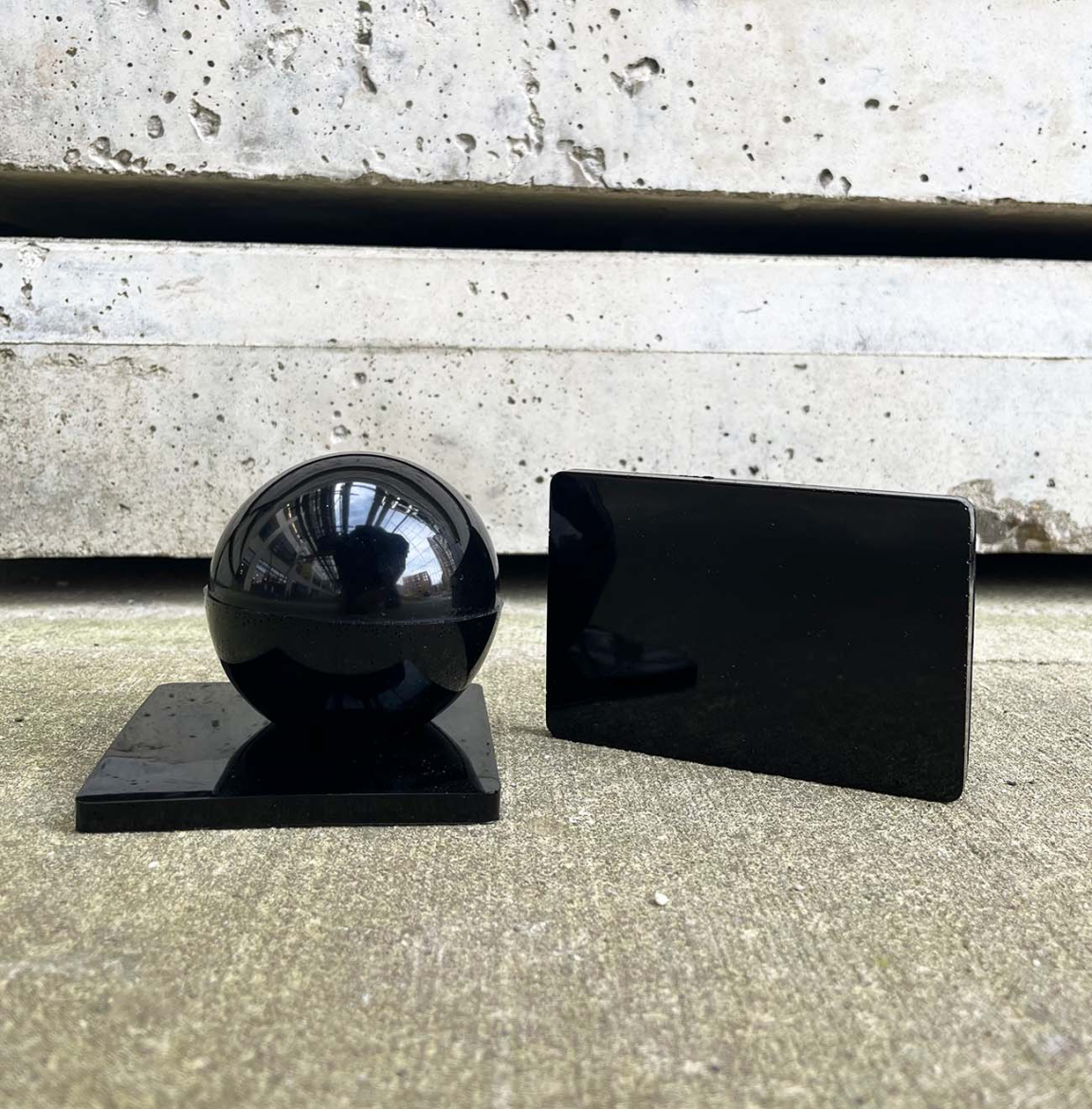
OurCarbon - Plastic
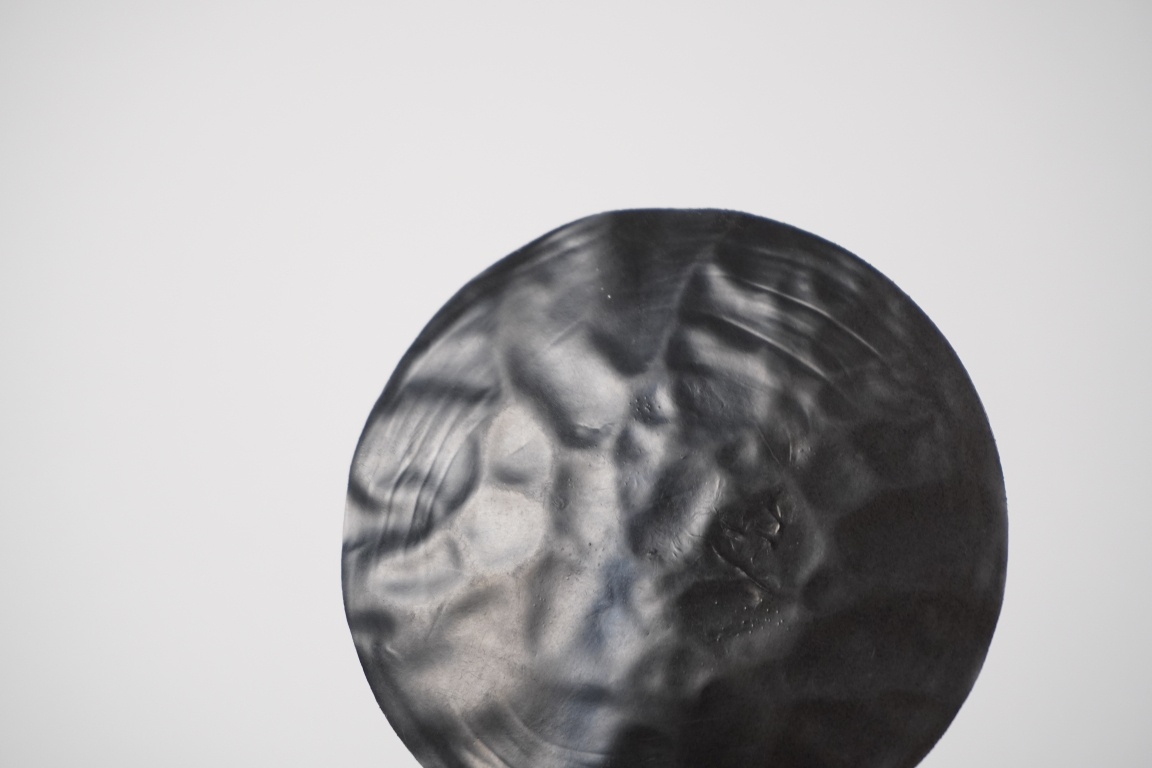
OurCarbon - EcoResin
Where do you source your would-be waste?
"We actually don’t source the material per-se. Wastewater municipalities have gone through a very long and thorough process of requesting proposals for new technologies to manage their waste, reviewing those proposals and finally purchasing the BFT system and installing it directly onto their treatment plant site. While they now own our machines, we take on the responsibility of collecting the OurCarbon produced from the system and applying it to industries to upcycle the waste stream. This way we don’t have any transport costs or emissions, and we get to fit right into the wastewater footprint."
How will your process scale up to support more businesses?
"We’re excited to be scaling very quickly at the moment! In 2021, we were contracted to build over 20 BioDryers/Pyrolysis machines in USA and Europe. All of these installations will work with biosolids as their feedstocks and will allow us to produce more OurCarbon to satisfy growing demand."
What can businesses do to take the first steps in becoming more sustainable?
"Oof, that’s a big question! If there’s one thing we’ve seen first hand during this project it’s that small changes in a supply chain can have huge effects on a product or company’s overall impact. We’ve got a lot to fix, not a lot of time, and maybe most detrimental; a lot of noise out there confusing people about what is really making an impact. I think companies need to close loops on their supply chain, consider every ingredient in their products, and treat end of life just as seriously as they do material sources."
Have you encountered any blockers to businesses adopting your systems?
"It’s hard to imagine after 10 years of work, but within the wastewater world Bioforcetech is still seen as a ‘new technology.’ Wastewater treatment requires large amounts of taxpayer dollars to create processing infrastructure that will meet the demand of a growing population under difficult regulation for decades. This makes the industry extremely slow to adopt new technologies for fear of spending a lot of their citizen’s money on a technology that may not fit the bill.
"At the same time, upcoming regulations on contamination and landfilling of organics is leading the industry to see a need to change very quickly. It has been a long road since the start of Bioforcetech, but the team’s hard work has proven to the industry that their tech is really capable of stepping up to the challenge."
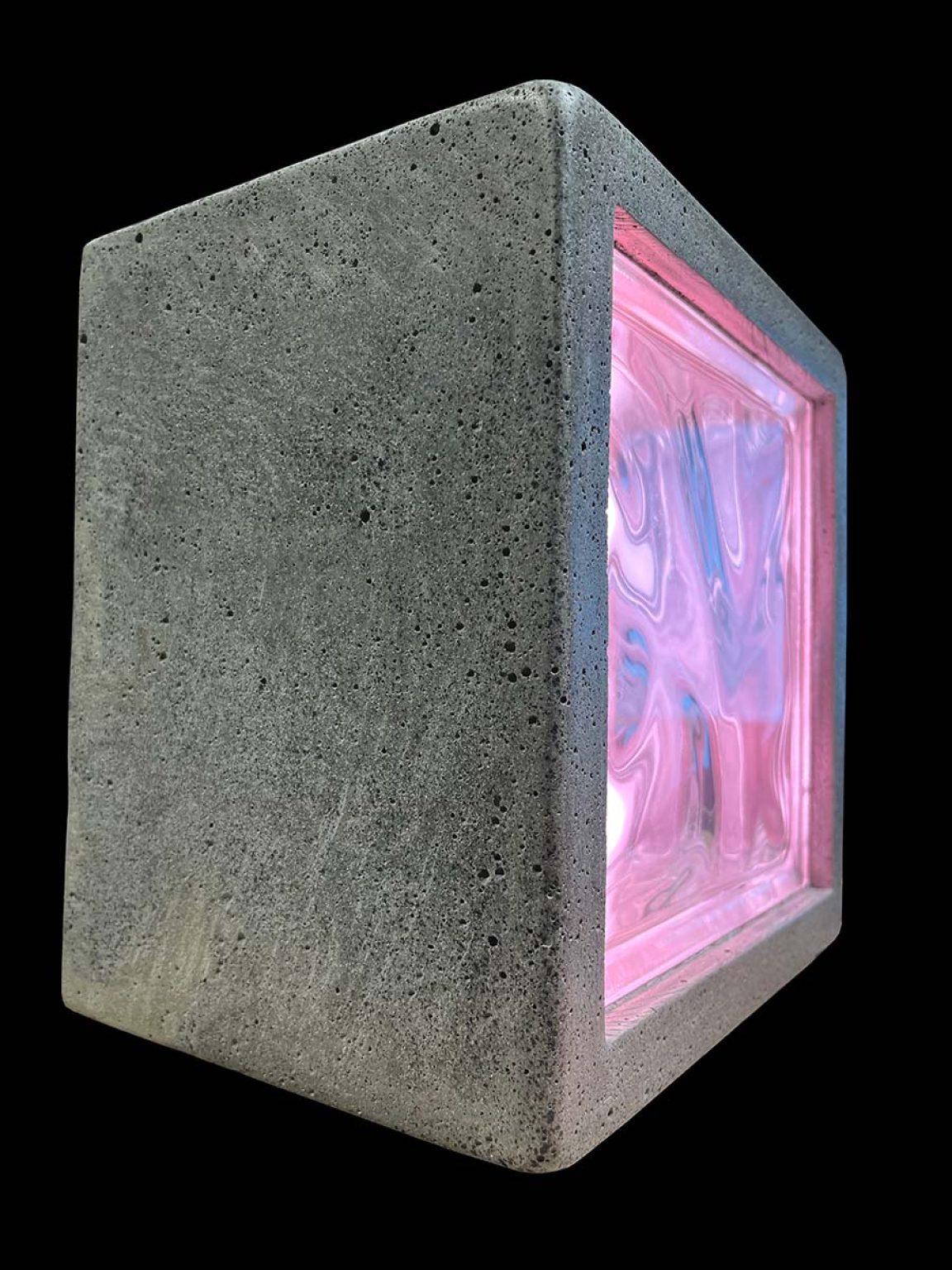
OurCarbon Concrete - Niles Fromm
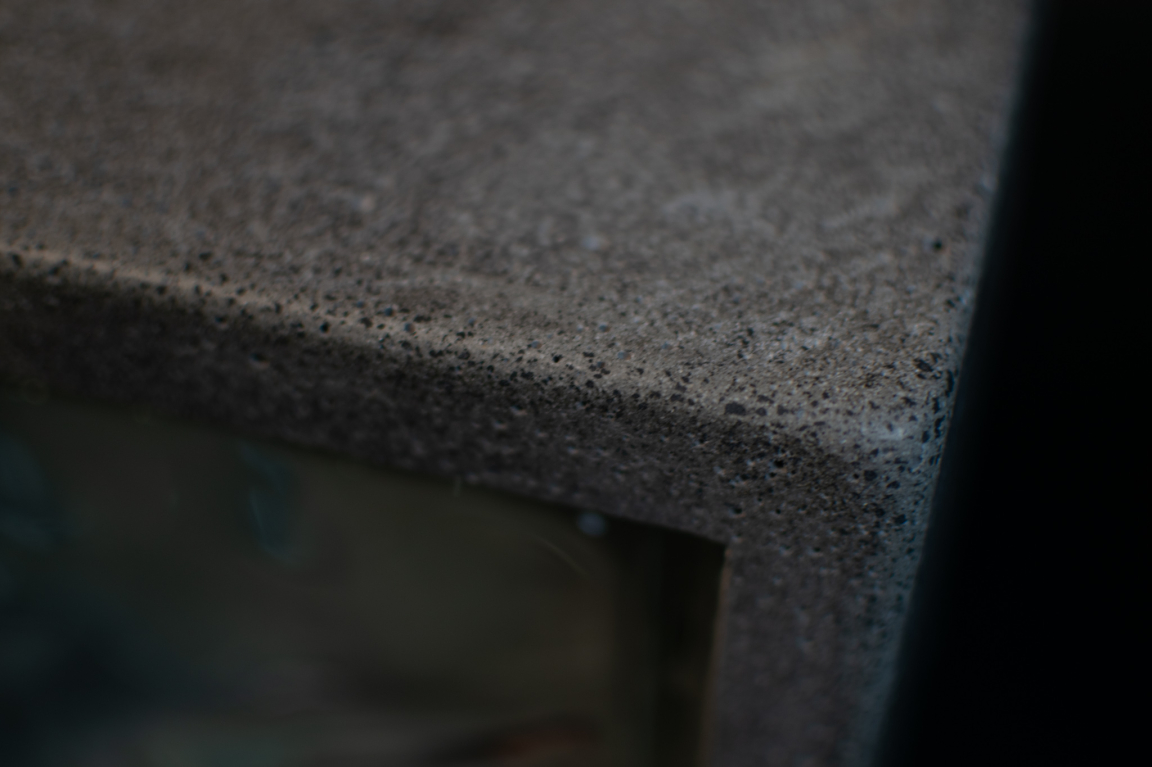
OurCarbon Concrete - Niles Fromm
What are you currently working on?
"We are currently working on exploring the very exciting world of masterbatch plastic nurdles! (nurdle also happens to be our favourite word) These tiny little pieces of pigmented polymer are the way that many of the things around us are coloured. When the keyboards on our laptops are injection moulded, or the fibres in our ski coats are extruded, they have all been coloured by a small quantity of coloured nurdles which are mixed into a polymer. Pigments can be masterbatched in every polymer you can imagine; compostable plastics such as PHA and PLA, recycled plastics such as rPET as well as the more traditional plastics such as PVC, PP, and HDPE.
"By using OurCarbon to pigment these polymers we’re able to replace the world's most commonly used black pigment, known as Carbon Black, which is made by burning fossil fuels and collecting the soot that forms as a result. Needless to say, it is an amazing opportunity to clean up the way we colour many of the objects we interact with every day.
"A few of the other exciting things we’re working on are utilising OurCarbon as a concrete additive which, if testing continues where it’s going, could give concrete a neutral (or even negative!) carbon footprint. We’ve also just partnered with Virus Inks to create a black screenprinting ink called RethINK Black, which can be used on nearly every material you can think of from paper to textiles and even plastics. Their ink media is water based and the ingredients are 80% biobased, making it a really sustainable combo with OurCarbon."
And what’s next?
"WORLD DOMINATION! Just kidding. We’re really excited about continuing to grow within a sustainable community and look forward to new collaborations! Every industry that we introduce OurCarbon to has a ‘base’ form that they prefer the material to be in, whether it’s a powder, liquid concentrate, nurdle (still a great word), or the original granule the material comes out of our machines as. We’re looking forward to partnering with more industry partners to be able to deliver OurCarbon to manufacturers in each of these forms so that they can integrate OurCarbon right away..
"Now that we’re scaling the use of our material made of biosolids, we’re really interested in working with other waste feedstocks as well. There are many wet organic waste streams like kelp, agricultural waste and even chicken litter that could utilise our system to reduce the emissions and waste that would otherwise be produced. Each of these organic feedstocks will yield an OurCarbon biochar with unique properties which can be used to broaden the applications this material can be used for."
From The Ground Up will open this month at Material Source Studio, 1 Federation Street, Manchester. Further details will be announced in the coming week.